Understanding Mesh Filter Screens for Pumps
When it comes to maintaining the efficiency and longevity of pumps in various industrial applications, one crucial component often overlooked is the mesh filter screen. These screens play an essential role in protecting pumps from debris and contaminants, which can lead to costly repairs and downtime.
What is a Mesh Filter Screen?
A mesh filter screen is a filtering device made from woven or perforated material that allows fluids to pass through while capturing larger particles and debris. Typically made from stainless steel, nylon, or polyester, these screens come in various mesh sizes, which refer to the number of openings per linear inch. A finer mesh captures smaller particles; conversely, a coarser mesh allows for higher flow rates but might miss smaller contaminants.
Importance of Mesh Filter Screens in Pumps
In many pump applications, especially those involving water, chemicals, or petrochemicals, the presence of solid particles can significantly affect performance. Without proper filtration, debris can enter the pump and cause wear or damage to essential components like impellers and seals. Over time, this not only degrades pump efficiency but can also lead to catastrophic failures.
Moreover, accumulating debris can result in clogs, leading to increased energy consumption and reduced flow rates. By incorporating a mesh filter screen, operators can enhance the reliability of their pumping systems, prolong the life of equipment, and reduce operational costs by minimizing maintenance and repairs.
Types of Mesh Filter Screens
There are various types of mesh filter screens tailored to different applications. Some of the common types include
mesh filter screen for pump
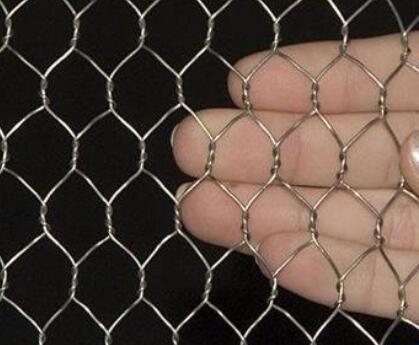
1. Basket Filters These are used in applications where large volumes of liquid need to be filtered. A basket filter is cylindrical and has a fine mesh lining to trap particles while allowing fluid to flow freely.
2. Inline Filters Installed directly into the pipeline, these filters ensure continuous filtration of the fluid. They take up less space than basket filters and are ideal for installations where space is limited.
3. Strainer Filters Commonly used in industrial settings, strainer filters provide coarse filtration and are primarily designed to protect pumps and valves from larger debris.
4. Self-Cleaning Filters For high-flow applications, self-cleaning filters utilize automated systems to remove trapped debris, ensuring minimal downtime and maintaining system efficiency.
Choosing the Right Mesh Size
Selecting the appropriate mesh size for a filter screen is critical. Using a mesh that is too fine can cause excess pressure drop, reducing pump efficiency and performance. On the other hand, a mesh that is too coarse may not adequately protect the pump, allowing damaging particles to pass through. Therefore, it's essential to consider the specific application, fluid characteristics, and potential contaminants to choose the right mesh size.
Conclusion
In conclusion, mesh filter screens are a vital component of pump systems across various industries. They provide protection against debris and contaminants, enhancing the efficiency and longevity of pumps while reducing the need for maintenance. By understanding the different types of filter screens and selecting the appropriate mesh size, operators can ensure optimal performance and reliability in their pumping operations. Investing in quality mesh filter screens is not just a maintenance task; it’s a strategic decision towards operational excellence and cost savings.