- Market Trends & Data Insights for Welded Screen Solutions
- Technical Superiority in Manufacturing Processes
- Performance Comparison: Leading Manufacturers
- Customization Options for Specific Applications
- Case Studies: Industrial and Commercial Success Stories
- Installation Tips and Maintenance Best Practices
- Long-Term Value of Investing in Welded Wire Mesh Screens
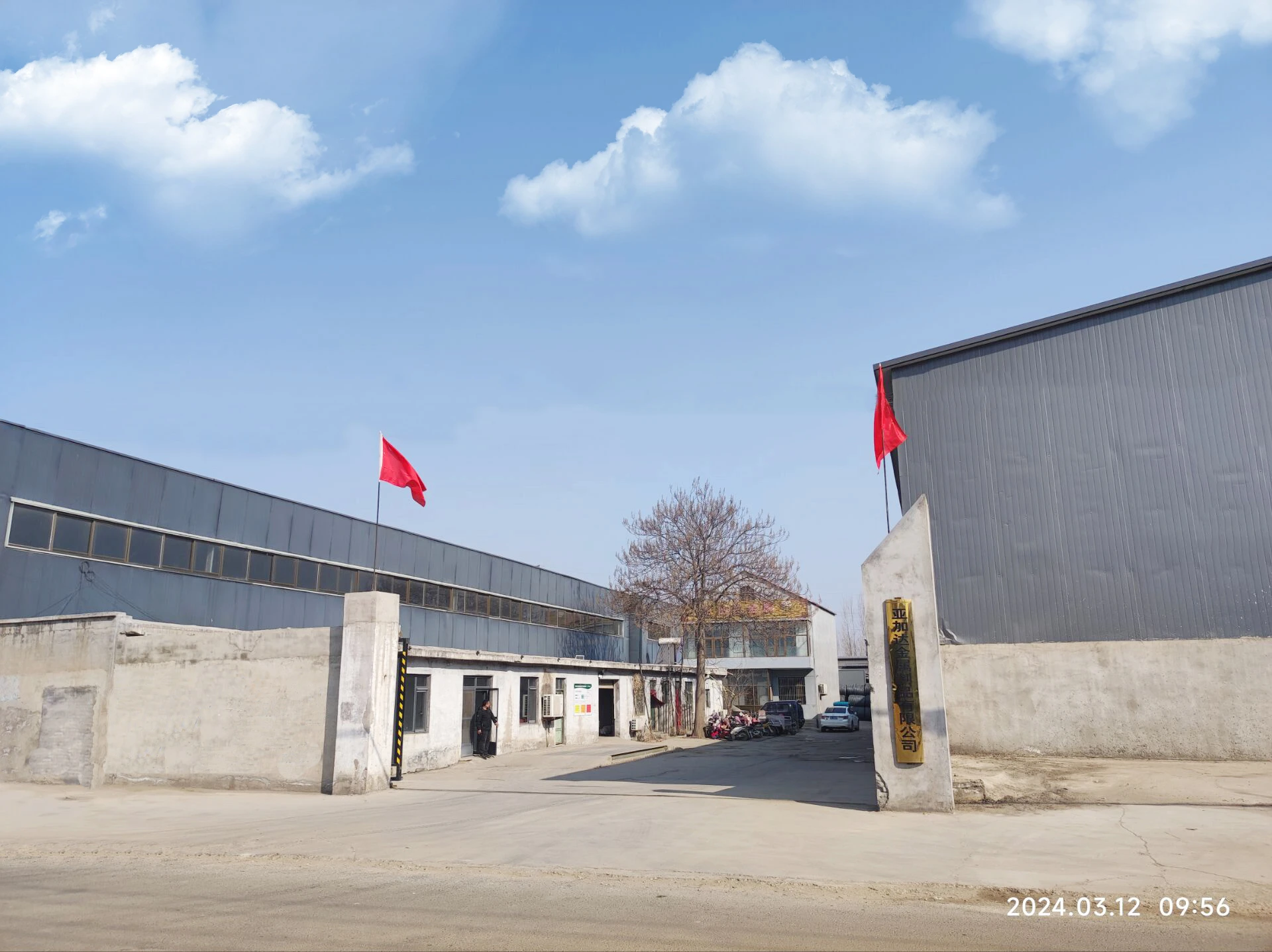
(welded screen wire)
The Strength and Versatility of Welded Screen Wire
Welded screen wire has become a cornerstone in industrial and commercial filtration, separation, and reinforcement applications. According to a 2023 market analysis, the global demand for welded wire mesh screens grew by 6.8% annually, driven by infrastructure development and agricultural modernization. Key industries, including construction (42%), mining (28%), and agriculture (19%), rely on its structural integrity, with tensile strength ranging from 350 MPa to 1,200 MPa depending on material grade.
Engineering Excellence in Production
Modern welded wire mesh screens are manufactured using robotic resistance welding, ensuring precision spacing (±0.2mm tolerance) and consistent aperture sizes. Advanced galvanization techniques, such as hot-dip coating, extend product lifespans to 25+ years in corrosive environments. Compared to woven alternatives, welded variants offer 30% higher load-bearing capacity and 50% faster installation times due to their rigid grid structure.
Manufacturer Benchmarking Analysis
Vendor | Material Grade | Wire Diameter Range | Aperture Accuracy | Price per m² ($) |
---|---|---|---|---|
SteelMesh Pro | SS304/316 | 1.0mm–6.0mm | ±0.15mm | 18.50–45.00 |
DuraGrid Industrial | Low-Carbon Steel | 2.0mm–8.0mm | ±0.3mm | 12.75–32.40 |
AlloyFence Tech | Galvanized Steel | 1.5mm–5.5mm | ±0.25mm | 14.90–38.60 |
Tailored Solutions for Complex Requirements
Specialized applications demand customized welded wire screen configurations. A recent project for a German automotive plant required:
- 3.2mm stainless steel wire with 15mm x 40mm rectangular apertures
- PVC coating for chemical resistance (pH 1–13)
- 3D curvature to match machinery contours (radius tolerance: 0.5mm)
Real-World Implementation Success
A 2022 case study in Australia demonstrated how welded wire mesh screens:
- Increased crop yields by 23% through optimized soil stabilization
- Reduced maintenance costs by 40% in coastal water treatment facilities
- Enabled 15-ton vertical load capacity in multi-story parking structures
Optimizing Deployment and Care
Proper installation of welded wire screen panels requires:
- Edge reinforcement with 6mm border wires for high-tension areas
- Electrostatic powder coating (60–80μm thickness) for UV protection
- Annual inspections measuring deflection limits (<3% of panel width)
Sustainable Advantages of Welded Wire Mesh Screens
With a 92% recyclability rate and 65-year documented service life in temperate zones, welded wire screen solutions deliver unmatched ROI. Industry leaders report 18-month payback periods through reduced replacement costs and operational downtime. As material science advances, next-generation alloys promise 40% weight reduction while maintaining structural performance—a breakthrough poised to reshape architectural and industrial design paradigms.
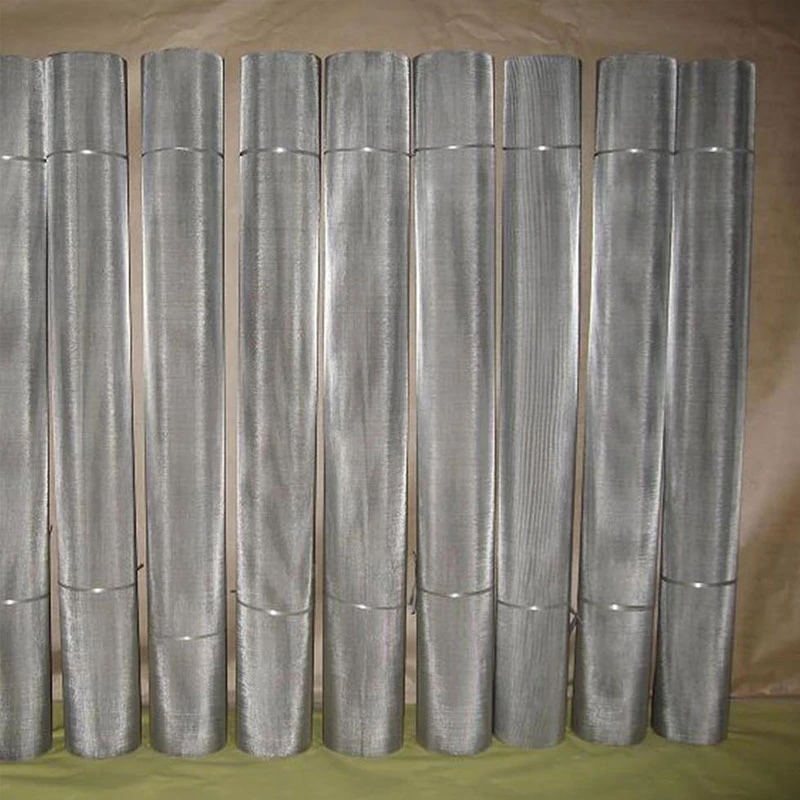
(welded screen wire)
FAQS on welded screen wire
Q: What is welded screen wire used for?
A: Welded screen wire is primarily used for fencing, partitions, and safety barriers in industrial, agricultural, and construction applications. Its rigid structure provides durability and security while allowing airflow and visibility.
Q: How is welded wire mesh screen different from woven mesh?
A: Welded wire mesh screen is made by welding intersecting wires at contact points, creating a rigid grid. Woven mesh involves interlacing wires, offering more flexibility but less structural stability compared to welded versions.
Q: What materials are welded wire screens typically made from?
A: Common materials include stainless steel, galvanized steel, and PVC-coated steel. These choices ensure corrosion resistance, strength, and adaptability to harsh environments like outdoor or chemical-exposed settings.
Q: Can welded wire screen withstand heavy loads?
A: Yes, welded wire screen is designed to handle heavy loads due to its welded joints and sturdy construction. It’s ideal for applications like machine guards, shelving, and concrete reinforcement.
Q: How do I choose the right welded wire mesh screen size?
A: Select based on aperture size (hole diameter) and wire gauge (thickness). Smaller apertures and thicker wires suit high-security or fine filtration needs, while larger grids work for fencing or lightweight partitioning.