Understanding Perforated Plates A Guide to Manufacturers and Applications
Perforated plates play a vital role across various industries, serving as essential components in processes ranging from filtration to structural applications. As demand for these versatile materials grows, manufacturers have continuously developed innovative techniques to meet the needs of different sectors. This article explores the significance of perforated plates, their manufacturing processes, and the factors to consider when choosing a manufacturer.
What Are Perforated Plates?
Perforated plates are flat sheets of material with a series of holes or openings of various sizes and configurations uniformly distributed across the surface. These plates can be made from various materials, including metals, plastics, and composites, which determine their suitability for specific applications. The unique combination of strength, weight, and air or fluid flow characteristics makes perforated plates a popular choice for architects, engineers, and designers.
Applications of Perforated Plates
1. Filtration One of the primary uses of perforated plates is in filtration systems. By regulating the size and shape of the holes, manufacturers can produce plates that effectively separate different substances in liquids and gases. They are widely used in wastewater treatment, food processing, and chemical industries.
2. Ventilation and Sound Absorption In construction and architecture, perforated plates are utilized in ceilings and walls to enhance ventilation and acoustics. The holes allow for airflow while reducing noise levels, making these plates ideal for public buildings, theaters, and offices.
3. Decorative Elements Beyond functional uses, perforated plates have become popular in interior design and architecture. They can serve as decorative panels, providing creative visual effects while maintaining functionality. Different patterns and hole sizes can convey unique design elements.
4. Industrial Applications In industries such as mining and construction, perforated plates are used in sorting and grading materials. Their strength and durability make them ideal for heavy-duty applications, including screening, separating aggregates, and supporting loads.
The Manufacturing Process
The process of manufacturing perforated plates involves several key steps
1. Material Selection Depending on the intended application, manufacturers choose appropriate materials. For instance, stainless steel is favored for its corrosion resistance, while aluminum may be selected for lightweight applications.
perforated plate manufacturers
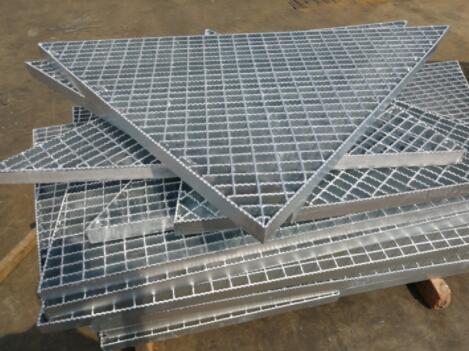
2. Hole Design The configuration of holes varies based on the final use. Computer-aided design (CAD) software is often utilized to create precise designs, ensuring accuracy and consistency.
3. Perforating The actual perforation can be achieved through multiple methods, including punching, laser cutting, or water jet cutting. Each method has its advantages; for instance, laser cutting allows for intricate designs, while punching is more efficient for high-volume production.
4. Finishing After perforation, the plates may undergo additional processes to enhance their properties. This can include bending, welding, coating, or surface treatment to improve durability and appearance.
Choosing a Perforated Plate Manufacturer
When selecting a manufacturer for perforated plates, consider the following factors
1. Experience and Expertise Look for manufacturers with a proven track record in producing high-quality perforated plates. Their experience can be indicative of their ability to meet your specific needs.
2. Customization Options Check if the manufacturer offers customization options for hole sizes, shapes, and plate dimensions. This flexibility can be crucial for meeting specific project requirements.
3. Quality Control A commitment to quality assurance is essential. Manufacturers should implement rigorous testing and inspection processes to ensure their products meet industry standards.
4. Lead Times and Pricing Evaluate the manufacturer's lead times and pricing structures. Competitive pricing is important, but it should not compromise quality or delivery timelines.
5. Customer Support Effective communication and support can significantly enhance your experience with a manufacturer. Look for companies that offer responsive customer service to address your concerns.
Conclusion
Perforated plates are indispensable in various industries due to their versatility, functionality, and aesthetic appeal. Manufacturers play a crucial role in producing these plates, utilizing advanced technologies and adhering to strict quality standards. When selecting a manufacturer, consider experience, customization options, quality control, pricing, and customer support to ensure you choose a reliable partner for your perforated plate needs. Whether for filtration, noise reduction, or architectural design, the right perforated plate can make all the difference in your project’s success.