Hot Dip Wire An Overview of the Process and Applications
Hot dip wire refers to a process widely used in the metalworking industry, primarily for the purpose of coating steel wire with a layer of zinc. This process, known as hot-dip galvanizing, enhances the wire's resistance to corrosion, improves its durability, and extends its service life. The method involves submerging the wire into molten zinc, which adheres to the surface, creating a protective barrier against environmental factors.
The hot dip wire process begins with preparing the steel wire. It is first cleaned to remove any impurities, such as oil, dirt, or oxide layers. This is typically achieved through a series of degreasing, pickling, and rinsing steps. After the wire is thoroughly cleaned, it is dried to ensure that no moisture remains, as this could negatively affect the bonding of the zinc coating.
Once the surface preparation is complete, the wire is drawn through a bath of molten zinc. The temperature of the zinc bath usually ranges between 450°C to 480°C (842°F to 896°F). During this immersion, the zinc reacts with the iron in the steel to form a series of zinc-iron alloy layers, which are interspersed with pure zinc. This multi-layer structure is crucial as it provides excellent corrosion resistance while maintaining the physical properties of the wire.
hot dip wire
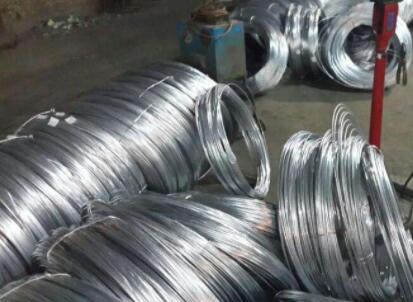
After the wire is removed from the zinc bath, it is allowed to cool, and any excess zinc is removed to achieve the desired coating thickness. The control of the coating thickness is paramount; it can typically range from 50 to 600 grams per square meter, depending on the specific application and environmental conditions where the wire will be used.
Hot dip wire has numerous applications across various industries. One of its most common uses is in the construction sector, where it is utilized in the manufacture of fencing, wire meshes, and reinforcement bars. The enhanced corrosion resistance provided by the zinc coating makes these products suitable for outdoor use and protects them from rust and other environmental damages. Additionally, hot dip wires are used in the production of various automotive components, agricultural machinery, and electrical transmission lines.
The advantages of using hot dip wire are numerous. Not only does the galvanization process prolong the lifespan of the wire, but it also reduces maintenance costs over time. Furthermore, the process is environmentally friendly, as zinc is a naturally abundant and recyclable material.
In conclusion, hot dip wire processing is an essential technique in metallurgy, offering significant benefits in terms of corrosion protection and durability. As industries continue to evolve and demand higher quality materials, the significance of hot dip wire only stands to increase, solidifying its role in modern manufacturing practices.