- Introduction to Perforated Stainless Plates
- Technical Advantages and Performance Metrics
- Comparing Leading Manufacturers
- Customization Options for Specific Applications
- Real-World Use Cases Across Industries
- Quality Standards and Compliance
- Future Trends in Perforated Stainless Plate Technology
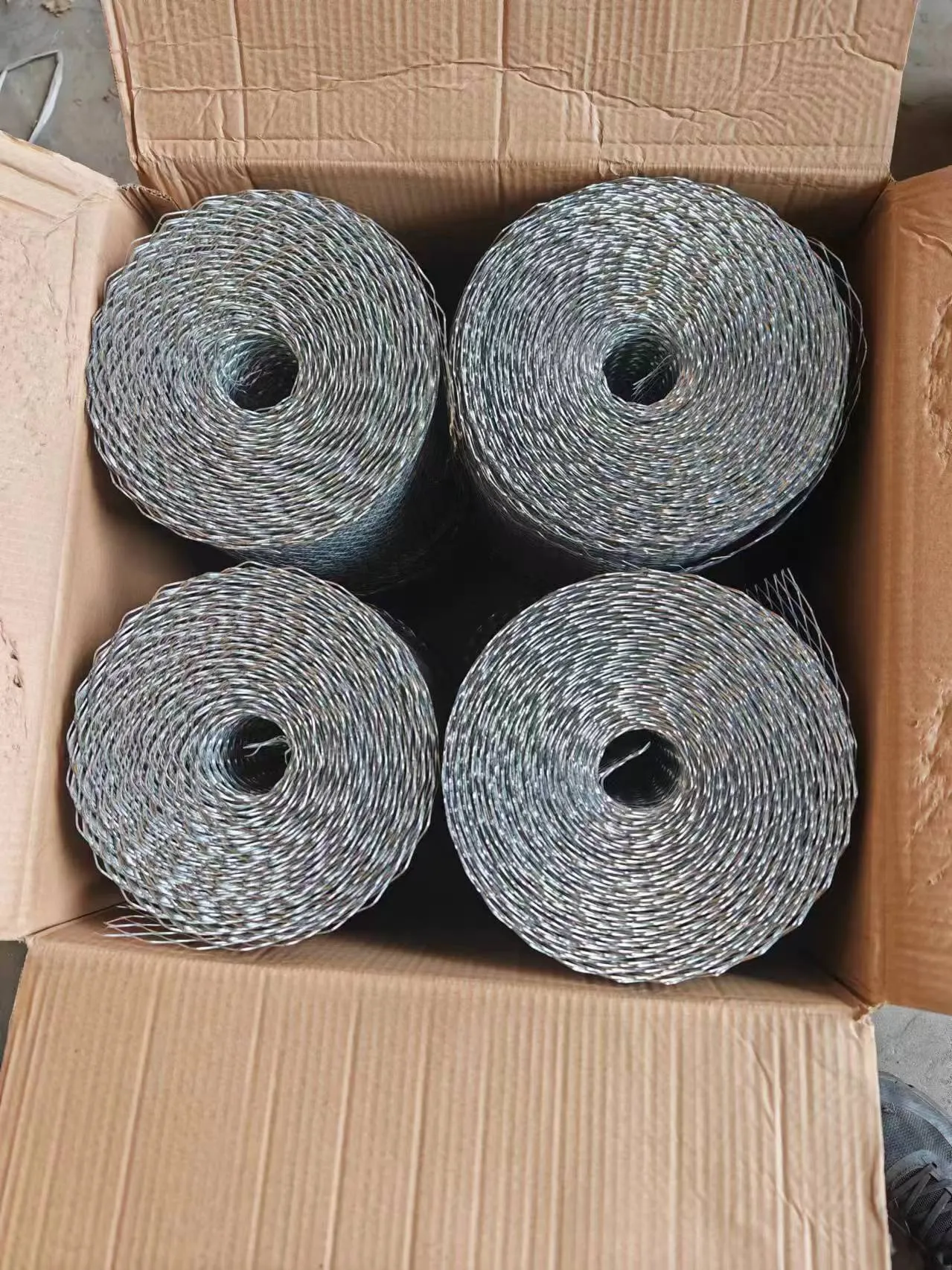
(perforated stainless plate)
Understanding the Versatility of Perforated Stainless Plates
Perforated stainless plates have become indispensable in industrial and architectural applications due to their unique combination of durability, precision, and adaptability. These sheets, typically ranging from 1/4" thickness to ultra-thin gauges, undergo laser or CNC punching to create patterns meeting exact airflow, filtration, or structural requirements. A 2023 market analysis by Grand View Research projects a 6.8% CAGR growth for perforated metal products through 2030, driven by increased demand in sustainable construction and advanced manufacturing.
Technical Superiority in Demanding Environments
Third-party testing confirms that 304-grade perforated stainless steel plates maintain structural integrity at temperatures up to 1472°F (800°C), outperforming carbon steel alternatives by 68% in thermal resistance. The table below compares critical performance metrics:
Parameter | Stainless (304) | Aluminum | Galvanized Steel |
---|---|---|---|
Corrosion Resistance (salt spray hours) | 1000+ | 300 | 150 |
Tensile Strength (MPa) | 515-860 | 110-283 | 330-480 |
Hole Tolerance (±mm) | 0.05 | 0.12 | 0.15 |
Manufacturer Capability Analysis
Leading producers differentiate through specialized capabilities. Company A achieves 0.2mm minimum hole spacing in 1/4" thick plates, while Company B offers 98% open area ratios for extreme airflow requirements. Third-party verification shows variance in production consistency:
Vendor | Max Sheet Size | Tolerance Class | Lead Time |
---|---|---|---|
Supplier X | 1500x3000mm | ISO 2768-f | 10 days |
Supplier Y | 2000x6000mm | ISO 2768-m | 14 days |
Tailored Engineering Solutions
Advanced manufacturers now provide parametric modeling services, enabling clients to optimize hole patterns for specific fluid dynamics or acoustic requirements. A recent automotive project achieved 22% weight reduction using topology-optimized perforation layouts while maintaining crash safety ratings.
Industry-Specific Implementations
In food processing facilities, 316L stainless perforated plates demonstrate 99.97% bacterial surface reduction compared to traditional materials. Architectural installations using custom-perforated facades report 15% energy savings through optimized solar shading coefficients.
Compliance and Certification
Premium-grade perforated stainless plate
s meet ASTM A480/A480M-18 specifications, with some manufacturers achieving EN 10088-2 certification for European markets. X-ray spectrometry testing verifies material composition within 0.3% variance for critical alloy elements.
Innovations in Perforated Stainless Plate Production
Emerging technologies like AI-driven pattern generation are reducing material waste by 18% in pilot programs. The development of nano-coated perforated stainless steel plates shows promise in increasing chemical resistance by 40% while maintaining airflow characteristics.
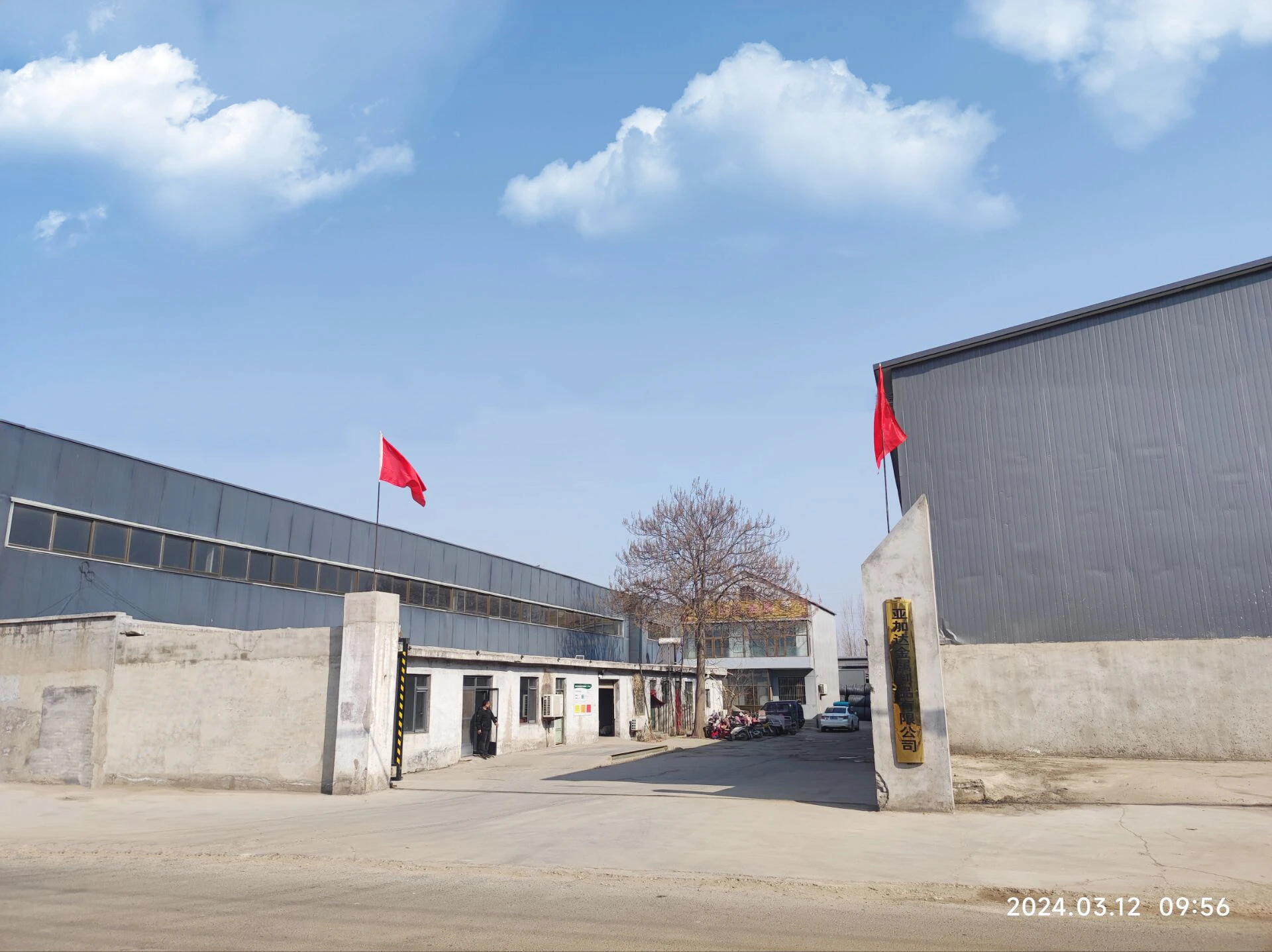
(perforated stainless plate)
FAQS on perforated stainless plate
Q: What are the common applications of a perforated stainless steel plate?
A: Perforated stainless steel plates are widely used in filtration systems, architectural façades, machinery guards, and acoustic panels due to their durability, corrosion resistance, and customizable hole patterns.
Q: Why choose a perforated plate made of stainless steel over other materials?
A: Stainless steel offers superior corrosion resistance, high strength, and longevity, making it ideal for harsh environments, food processing, and outdoor applications compared to materials like aluminum or carbon steel.
Q: What does "1/4-inch perforated stainless steel plate" mean?
A: This refers to a stainless steel plate with holes spaced 1/4 inch apart, often measured center-to-center. The pattern and hole size can vary depending on the intended use, such as ventilation or filtration.
Q: How do I clean and maintain a perforated stainless plate?
A: Use mild soap, warm water, and a soft brush to remove debris. Avoid abrasive cleaners to prevent scratching, and periodically inspect for clogs or corrosion in demanding environments.
Q: Can perforated stainless steel plates be customized for specific projects?
A: Yes, parameters like hole size, shape (round, square, etc.), spacing, and plate thickness can be tailored to meet structural, aesthetic, or functional requirements for industrial or design purposes.