Understanding Wire Filter Screens A Comprehensive Overview
In various industrial applications, the importance of clean and filtered materials cannot be overstated. One of the key components in achieving this cleanliness is the wire filter screen. These screens play a crucial role in filtering out unwanted particles from various liquids and gases, ensuring that systems operate efficiently and without contamination. This article delves into the significance, types, applications, and maintenance of wire filter screens.
Significance of Wire Filter Screens
Wire filter screens serve as barriers that retain larger particles while allowing smaller particles and fluids to pass through. Their vital function is seen across multiple industries including water treatment, food and beverage processing, pharmaceuticals, and more. By preventing contaminants from entering systems, these filters enhance the quality of the end product, protect machinery from damage, and comply with industry regulations. The right wire filter screen can dramatically improve operational efficiency and prolong the lifespan of equipment, making them an invaluable asset.
Types of Wire Filter Screens
Wire filter screens come in various types, each designed to cater to specific filtering needs. The key categories include
1. Woven Wire Mesh This is made from woven metal wires, creating a mesh structure that provides adjustable openings. It's versatile and can be customized to different specifications based on the size and type of particles needing filtration.
2. Perforated Metal Screens These screens consist of a solid sheet of metal with punctured holes that allow fluid or gas to pass through while filtering solids. They are particularly strong and can handle high flow rates.
3. Sintered Wire Mesh Sintered filters are created through the process of fusing together multiple layers of mesh. They provide excellent strength, durability, and a higher filtration precision, suitable for fine particle separation.
wire filter screen
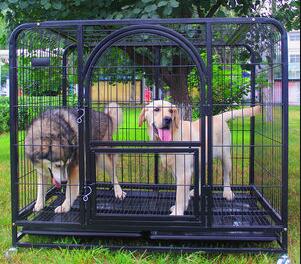
4. Lenticular Filters A unique design that allows for efficient filtration by stacking multiple membranes. These filters are often used in applications requiring sterile filtration.
Applications of Wire Filter Screens
The applications of wire filter screens span numerous sectors. In the water and wastewater treatment industry, these screens ensure that larger solids are removed, helping to purify drinking water and treat sewage. In the food processing sector, they are employed to filter juices, oils, and other liquids, ensuring that the final products are free from impurities.
In pharmaceuticals, wire filter screens are crucial during manufacturing processes to meet stringent hygiene and safety standards. Moreover, in the petrochemical industry, they play a critical role in the filtration of fuels and lubricants, protecting sensitive machinery from harmful contaminants.
Maintenance of Wire Filter Screens
To ensure optimal performance, regular maintenance of wire filter screens is essential. This involves routine inspections to check for wear and tear, cleaning procedures to remove buildup from the surfaces, and replacements when necessary. Over time, debris and particles can clog the mesh or perforated areas, leading to reduced flow rates and eventual system failure if not addressed.
Proper maintenance not only enhances the lifespan of the wire filter screens but also minimizes downtime, saves costs, and maintains the quality of the filtered product.
Conclusion
In conclusion, wire filter screens are indispensable components in a wide range of industrial processes. Their ability to filter out unwanted particles, preserve product quality, and enhance system performance makes them essential in various applications. Understanding the different types available and their appropriate maintenance can lead to improved operational efficiency and sustainability in industrial practices. Whether in water treatment, food processing, or pharmaceuticals, the role of wire filter screens continues to grow in significance as industries strive for cleaner, safer, and more efficient processes.