Understanding the Significance of 16% No Gi Wire in Modern Fabrication
In the ever-evolving world of manufacturing and fabrication, materials play a pivotal role in determining the efficiency of production processes and the quality of the final product. Among these materials, 16% No Gi Wire has emerged as a significant choice for various applications. Let’s explore what this wire is, its characteristics, advantages, and its impact on industries today.
Firstly, it’s essential to clarify what we mean by 16% No Gi Wire. The term No Gi typically refers to a type of wire that does not undergo galvanization, meaning it is not coated with a layer of zinc. This is significant as galvanization can protect the wire from corrosion but may affect its weldability and overall performance depending on the intended use. The 16% might refer to a specific alloying element or composition necessary to enhance the wire's properties. Though typically associated with galvanized wire, non-galvanized variants of wire are often favored in situations where coatings may interfere with operations or where a specific finish is required.
Understanding the Significance of 16% No Gi Wire in Modern Fabrication
Another notable feature of 16% No Gi Wire is its fantastic weldability. Unlike some other wire types, which may be challenging to weld due to coatings or incompatible materials, 16% No Gi Wire is often easier to work with. This property not only speeds up the production process but also allows for cleaner and more reliable joints, reducing the risk of structural failures.
16 no gi wire
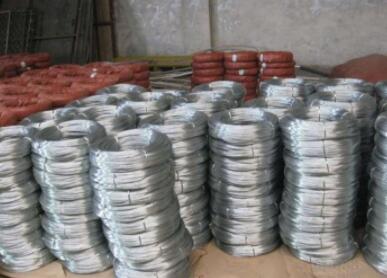
Additionally, the absence of galvanization may also make 16% No Gi Wire more environmentally friendly in certain applications. As sustainability becomes a significant concern for many industries, opting for materials that do not undergo extensive chemical processing can positively impact overall ecological footprints.
In terms of industries that benefit from 16% No Gi Wire, the construction and automotive sectors lead the charge. In construction, the wire is invaluable for tasks such as tying rebar, creating facades, and reinforcing structures that demand high-strength materials. Similarly, the automotive industry uses this wire in various applications including body frames, where strength and durability are paramount.
However, it is essential to acknowledge the potential drawbacks of using 16% No Gi Wire. The absence of a protective coating may expose the wire to conditions that could result in rust or corrosion, particularly in humid or corrosive environments. Thus, it’s vital for industries to consider the application and environment before choosing to implement this wire type.
In conclusion, 16% No Gi Wire stands out as a versatile material that meets the high demands of modern manufacturing and fabrication. Its remarkable strength, excellent weldability, and reduced environmental impact make it an attractive choice across various sectors. Nevertheless, as with all materials, understanding its properties and potential limitations is crucial for ensuring optimal usage and success in construction, automotive, and manufacturing applications. As industries continue to innovate, the role of materials like 16% No Gi Wire will undoubtedly remain significant in shaping the future of fabrication.