Understanding Hot Dip Galvanized Wire Manufacturers
Hot dip galvanized wire is an essential product used across various industries, known for its corrosion resistance and durability. The process of hot dip galvanization involves coating steel or iron wire with a layer of zinc, which protects it from rust and extends its life. This makes it a popular choice for construction, fencing, agriculture, and many other applications. To appreciate the importance of this product, we must first look at the manufacturers involved in its production.
What is Hot Dip Galvanization?
Hot dip galvanization is a method where steel wire is immersed in molten zinc. The high temperature causes a metallurgical reaction between the zinc and the iron in the wire, resulting in the formation of a robust zinc-iron alloy. This coating provides excellent protection against atmospheric conditions, making it ideal for outdoor applications. The process not only enhances the aesthetic appeal of the wire but also significantly improves its strength and lifespan.
The Role of Manufacturers
Manufacturers of hot dip galvanized wire play a crucial role in ensuring the quality and reliability of the final product. They are responsible for the entire production process, from sourcing raw materials to delivering finished goods. The quality of the wire depends on the expertise of the manufacturers and their adherence to industry standards.
1. Raw Material Sourcing The first step in the manufacturing process involves procuring high-quality steel or iron. Reputable manufacturers ensure that they source their materials from trusted suppliers, which is vital for achieving a durable final product.
2. Manufacturing Process After the raw materials are ready, manufacturers process the wire through various stages, including drawing, cleaning, and coating. Each stage must be meticulously handled to prevent any defects that could compromise the wire’s integrity.
hot dip galvanized wire manufacturers
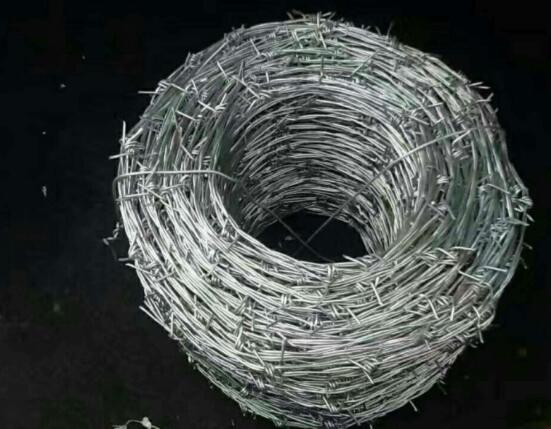
3. Quality Control Established manufacturers employ rigorous quality control measures to ensure that the coated wire meets specific standards. This often involves testing for thickness, adhesion, and corrosion resistance, ensuring that the wire will perform effectively in its intended application.
4. Customization and Variety Different industries have unique needs, and many manufacturers offer customized solutions. This can include various wire gauges, coatings, and additional treatments to meet specific requirements. A wide range of products allows customers to find exactly what they need for their projects.
5. Sustainability Practices As environmental concerns grow, many manufacturers are adopting sustainable practices. By minimizing waste and reducing energy consumption during production, they not only lower their carbon footprint but also appeal to environmentally-conscious consumers.
Global Market Insights
The global market for hot dip galvanized wire is rapidly expanding, driven by increased demand from construction and agricultural sectors. Countries such as China, India, and the United States are significant players, contributing to a substantial portion of the market. Manufacturers in these regions are continuously innovating, improving their processes, and developing advanced coating techniques to enhance corrosion resistance further.
As demand grows, manufacturers that invest in technology and maintain high standards of quality and sustainability will likely lead the market. This competitive landscape encourages continual improvement and innovation within the industry.
Conclusion
Hot dip galvanized wire manufacturers are at the forefront of producing a vital material that meets the demands of various sectors. Their commitment to quality, innovation, and sustainability shapes the future of the industry and ensures that customers receive a product that offers durability and performance. Understanding the processes and challenges these manufacturers face provides valuable insight into the importance of high-quality galvanized wire in our everyday lives.