- Introduction to iron winding wire
: importance and main uses - Technical characteristics and performance metrics
- Comparison of major manufacturers with a detailed data table
- Customization options: straight cut iron wire and U type iron wire
- Real-world application scenarios
- Quality assurance, certifications, and logistics
- Future prospects for iron winding wire and concluding insights
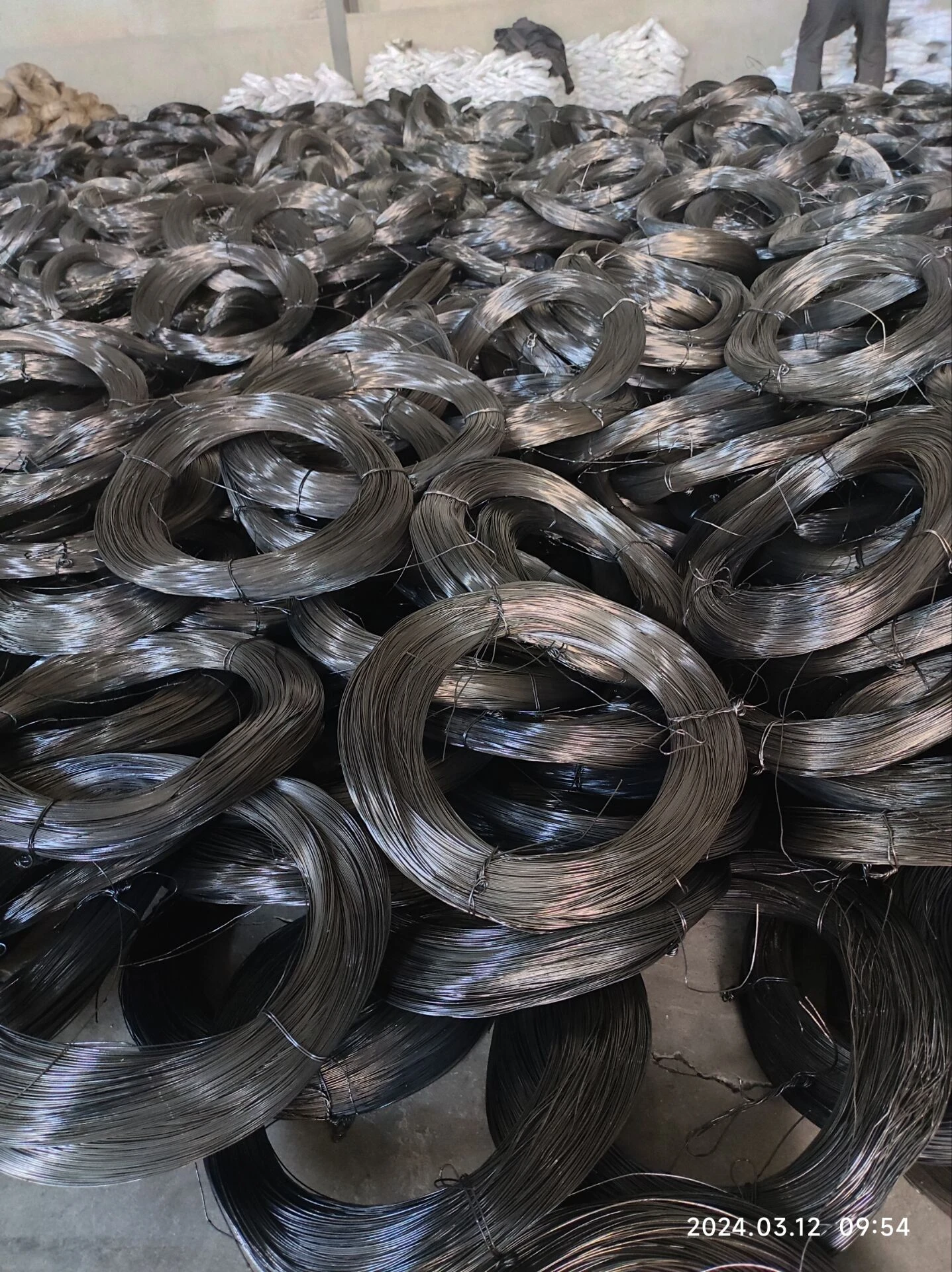
(iron winding wire)
Comprehensive Overview of Iron Winding Wire in Modern Industry
Iron winding wire stands as a critical component in the world of electrical engineering, construction, and manufacturing. Its primary function involves creating electrical coils, electromagnets, solenoids, and various forms of windings in motors and transformers. This versatility has secured its status as a foundational material, with a global consumption estimated at over 500,000 metric tons annually. The unique mechanical and conductive properties of iron winding wire deliver an optimum balance between durability and electrical performance, making it favored both in large-scale industrial applications and intricate electronic devices. Straight cut iron wire and U type iron wire variants enhance its utility, allowing manufacturers to meet highly specialized requirements across different sectors. With increasing trends toward energy efficiency and device miniaturization, demand for innovative winding wire continues to grow at a projected CAGR of 7.2% through 2030.
Technical Characteristics and Performance Metrics
High-performance iron winding wire is defined by several key criteria, including tensile strength, electrical resistance, surface finish, and dimensional accuracy. The diameter typically ranges from 0.15 mm to 8 mm, with tolerances maintained within ±0.01 mm, depending on the application. Electrical resistivity values are commonly calibrated between 0.10 to 0.12 μΩ·m at room temperature, ensuring efficient current transmission while minimizing losses. Surface treatments may include zinc, copper, or nickel coatings, each enhancing corrosion resistance and solderability. The annealing process is crucial; it imparts flexibility, reduces brittleness, and achieves standardized mechanical properties. According to the International Electrotechnical Commission (IEC 60317) standards, iron winding wire should demonstrate a minimum elongation of 10% without visible cracks, ensuring resilience during repeated winding and bending operations. Additionally, environmentally conscious production processes now prioritize lead-free coatings and recyclable materials, aligning with global sustainability mandates.
Manufacturer Comparison and Data Table
Choosing a reliable iron winding wire supplier requires careful assessment of product quality, pricing, and logistics support. The table below compares three leading global manufacturers, focusing on critical parameters such as monthly production capacity, minimum order quantity (MOQ), standard grade options, and delivery times. This data offers valuable insights for procurement managers, design engineers, and OEMs seeking optimal partners for their winding wire needs.
Manufacturer | Monthly Capacity (metric tons) | MOQ (kg) | Wire Grade Range | Standard Lead Time (days) | Certifications | Global Delivery |
---|---|---|---|---|---|---|
Alpha Metals Inc. | 9,500 | 100 | Standard/Annealed/Zinc Plated | 21 | ISO 9001, RoHS, REACH | 60+ countries |
Wireform Technologies | 12,000 | 250 | Standard, U type, Straight cut | 18 | ISO 14001, UL, CE | 45+ countries |
SteelWound Ltd. | 8,200 | 50 | Custom Alloy, Ultra-Fine, Annealed | 28 | ISO 9001, SGS | Global |
As illustrated, while Alpha Metals Inc. delivers on scale and certification depth, Wireform Technologies excels in short lead times and specialized forms such as straight cut iron wire and U type iron wire. SteelWound Ltd. caters to niche, high-precision orders. These distinctions enable buyers to align procurement choices with both technical and logistic priorities.
Customization Options: Straight Cut Iron Wire and U Type Iron Wire
To meet specialized applications, customization of iron winding wire is a key industry offering. Straight cut iron wire is generally supplied pre-cut to predetermined lengths (commonly 300 mm to 1000 mm), enhancing assembly line efficiency in sectors like construction reinforcement, horticulture, and art installations. Its straightening and cutting processes are performed under strict control to ensure uniformity, edge safety, and tolerance precision, factored at ±2 mm per piece. U type iron wire is widely used in bundling, structural anchoring, and wire mesh framing. The characteristic pre-formed “U” reduces labor time as no further bending is required on-site. Custom U-bends can be ordered with leg lengths from 25 mm up to 700 mm and are available in coated, annealed, or bare finishes to address unique environmental or mechanical requirements. With advanced automation, leading factories now offer bulk packaging (up to 5,000 pieces per carton) with laser-printed traceability codes, underpinning quality control and batch management.
Application Scenarios and Industry Cases
Iron winding wire plays a transformative role in numerous industries. In transformer manufacturing, high-purity annealed winding wire with precise gauge control is integral to efficient coil production, directly influencing device performance and longevity. The automotive sector leverages both standard and U type iron wire forms in stator and rotor assemblies, supporting the rise of electric vehicles and hybrid systems. For telecommunications infrastructure, ultra-fine winding wire ensures minimal signal loss in relays and circuit protection devices. A leading case study from a European motor manufacturer reported a 12% reduction in overall coil failure after transitioning to high-precision, custom-coated iron wire, highlighting significant performance gains. Furthermore, in green energy, straight cut iron wire accelerates the installation of solar panel frames and mounting brackets, streamlining overall project workflows. In recent years, demand has also surged in the crafting and design industries where uniform, rust-resistant wire supports both function and aesthetics in modern creations.
Quality Assurance, Certifications, and Logistics Excellence
Rigorous quality assurance protocols are vital in the iron winding wire industry. Leading providers implement advanced non-destructive testing, digital microscopy, and inline resistance measurement to ensure batch-to-batch consistency and compliance. Comprehensive certifications such as ISO 9001 and ISO 14001 reinforce manufacturing discipline, while industry-specific accreditations (UL, CE, RoHS) ensure product eligibility for sensitive electronic, automotive, and construction uses. Modern ERP systems integrate traceability at every stage, from raw material sourcing through final shipment. Packaging innovations, including moisture-protective wraps and anti-static reels, reduce transit risk, preserving wire integrity. Shorter lead times, customs documentation expertise, and expansive global logistics networks guarantee uninterrupted supply even amid dynamic market shifts. As industries increasingly outsource component production, these certification and logistics benchmarks become decisive factors in supplier selection.
Future Prospects and Market Opportunities for Iron Winding Wire
As next-generation manufacturing trends push the boundaries of efficiency and miniaturization, the demand for advanced iron winding wire solutions is set to accelerate. Innovations in coating technologies and metallurgy will unlock new possibilities in conductivity and corrosion resistance, directly benefitting applications ranging from renewables to consumer electronics. The expanding adoption of straight cut iron wire and U type iron wire configurations further showcases market appetite for labor-saving, ready-to-use materials. Analysis projects sustained double-digit growth in Asia-Pacific and North American markets, supported by large-scale investments in infrastructure, mobility, and smart manufacturing. At the same time, sustainable sourcing and eco-friendly production will become non-negotiable standards, compelling suppliers to invest in cleaner processes and recyclable designs. Ultimately, organizations that align technical excellence, reliable delivery, and customer-centric customization will define the future of iron winding wire in a rapidly evolving industrial landscape.
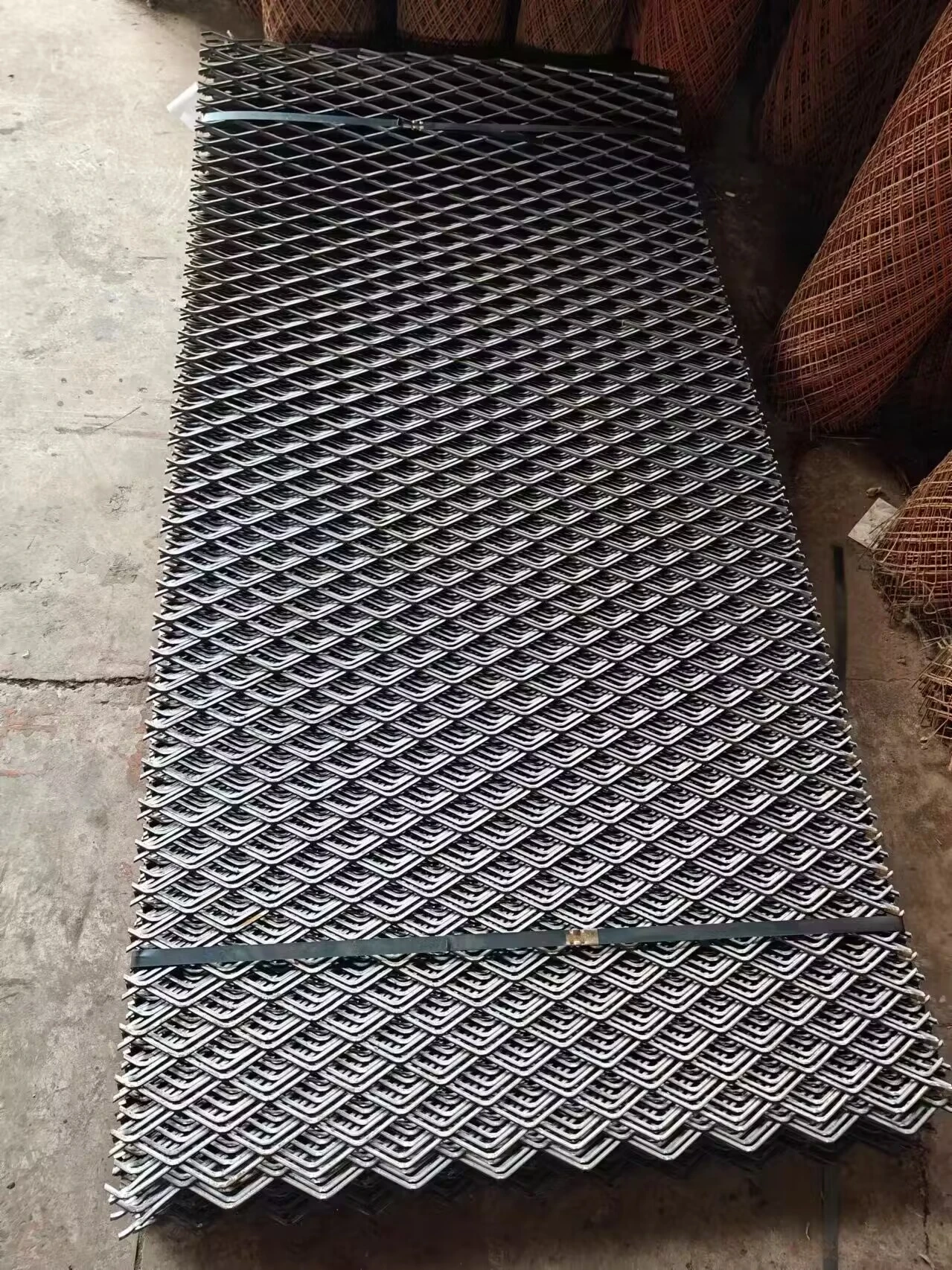
(iron winding wire)