Understanding Perforated Screen Sizes A Comprehensive Guide
Perforated screens have become a vital component in various industries, ranging from construction to manufacturing and even in environmental applications. The effectiveness of these screens largely depends on their design, specifically the sizes and patterns of the holes punched into them. In this article, we will explore the importance of perforated screen sizes, their applications, and the factors to consider when selecting the right size for your project.
What Are Perforated Screens?
Perforated screens are materials that have been punctured with holes in a structured pattern. The primary purpose of these screens is to allow the passage of air, liquid, or light, while filtering out larger particles. They are made from various materials, including metal, plastic, and composite materials, and are utilized in diverse applications such as architectural facades, filtration systems, and industrial machinery.
The Importance of Screen Sizes
The size of the holes in a perforated screen significantly influences its functionality. Different sizes cater to specific needs 1. Filtration In applications like wastewater treatment, smaller holes are necessary to prevent debris from passing through, ensuring that only clean water is filtered. 2. Ventilation Larger holes are beneficial in applications requiring ample airflow, such as in HVAC systems, where effective air circulation is paramount. 3. Aesthetics In architectural applications, the size and pattern of perforations can create visually appealing designs while maintaining functionality.
Factors to Consider When Choosing Perforated Screen Sizes
When selecting perforated screens, several factors must be considered
perforated screen sizes
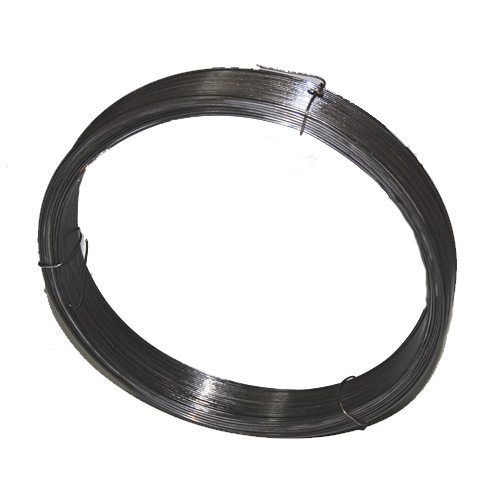
1. Purpose and Application Understand the primary function of the screen. If large particles need to be filtered out, smaller holes are required. Conversely, for applications where airflow is essential, larger holes may be more appropriate.
2. Material Different materials have varying strength and durability. Metal screens are typically chosen for their robustness, while plastic or composite screens may be used where weight is a concern.
3. Pattern and Spacing The arrangement of holes can impact performance. A uniform pattern may be suitable for consistent airflow, while a staggered pattern can enhance structural integrity and allow for better drainage in wet applications.
4. Regulations and Standards Some industries have specific regulations regarding perforated screens, especially in food processing or pharmaceutical applications. It’s crucial to adhere to these standards to ensure compliance and safety.
5. Environmental Considerations In applications involving exposure to harsh conditions, such as chemicals or extreme temperatures, selecting the right size and material is essential for longevity and effectiveness.
Conclusion
In conclusion, understanding perforated screen sizes is essential for anyone involved in industries that utilize these materials. The right size not only enhances the effectiveness of the screen but also ensures compliance and durability in various applications. Whether it's for filtration, ventilation, or aesthetics, careful consideration of the project's specific needs will lead to optimal performance and satisfaction. As technology advances, the design and manufacturing of perforated screens continue to evolve, offering even greater versatility and efficiency in meeting diverse industrial requirements.