Understanding Perforated Metal A Versatile Material for Modern Applications
Perforated metal, known for its unique pattern of holes and diverse applications, has become an increasingly popular choice in various industries. Characterized by its lightweight structure and strength, perforated metal is manufactured from sheets of metal that undergo a process of punching or perforating to create holes of different sizes and shapes. The resulting material provides aesthetic appeal, functional benefits, and versatility in design.
The Manufacturing Process
The manufacturing of perforated metal involves several steps, starting with the selection of the base material, which can be steel, aluminum, brass, or other metals. The metal sheets are then subjected to a perforating machine that uses dies to create accurate hole patterns. This process allows for customization in terms of hole size, spacing, and arrangement, making it possible to cater to specific project requirements.
Applications Across Industries
Perforated metal finds applications in various sectors, including construction, architecture, automotive, and consumer goods. In architecture, it is frequently used for facades, security screens, and decorative panels, providing both visual impact and functional benefits such as ventilation and light filtering. For example, buildings designed with perforated metal facades can achieve unique aesthetic qualities while enhancing energy efficiency through natural ventilation.
In the automotive industry, perforated metals are often utilized in mufflers, heat shields, and air filters, where weight reduction and structural integrity are crucial. Additionally, the decorative aspect of perforated metal is evident in products ranging from furniture to lighting fixtures, allowing designers to achieve innovative and stylish solutions that blend form and function.
Benefits of Perforated Metal
perforated metal harga
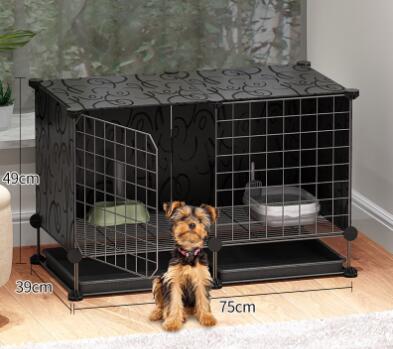
One of the primary advantages of perforated metal is its strength-to-weight ratio. Despite being lightweight, it maintains substantial durability, making it a reliable choice for numerous applications. Furthermore, the process of perforation can enhance sound absorption, which is particularly beneficial in environments where noise reduction is essential.
The versatility of perforated metal extends to its aesthetic qualities. It can be finished in various ways, including powder coating or anodization, allowing for customization in color and texture. This adaptability means that perforated metal can seamlessly integrate with a wide range of design styles, from modern to industrial.
Economic Considerations
When discussing the price or 'harga' of perforated metal, it is essential to consider several factors. The cost can vary significantly based on the type of metal used, the complexity of the perforation pattern, and the quantity ordered. While initial costs may be higher compared to standard metal sheets, the long-term benefits associated with durability, low maintenance, and energy efficiency often justify the investment.
Moreover, for businesses and projects requiring large volumes, purchasing perforated metal in bulk can yield significant savings. Engaging with reputable suppliers who offer competitive pricing for high-quality materials can further enhance project budgets without compromising on quality.
Conclusion
Perforated metal is a dynamic material that offers an excellent blend of strength, versatility, and aesthetic appeal. Its wide range of applications across diverse industries highlights its importance in modern design and engineering. As architectural trends continue to evolve, and industries seek innovative material solutions, perforated metal stands out as a suitable choice for both functional and decorative purposes. Understanding its benefits and cost factors can help designers and engineers make informed decisions when incorporating this remarkable material into their projects. Whether it's enhancing the visual impact of a building or improving the performance of an automotive part, perforated metal continues to prove its worth in today's manufacturing landscape.