Understanding Vibrating Screen Mesh A Key Component in Material Separation
Vibrating screens are crucial in various industries, including mining, construction, and recycling. They serve the essential function of separating materials based on size, ensuring that the correct particle fraction gets processed further. A pivotal element of vibrating screens is the mesh, which plays a vital role in the efficiency and effectiveness of the separation process. In this article, we will delve into what vibrating screen mesh is, its types, and its importance in different applications.
What is Vibrating Screen Mesh?
Vibrating screen mesh, also known simply as screen mesh or sieve, is a component that consists of woven wire or synthetic material designed to separate bulk materials by size. The mesh is typically mounted on a vibrating structure that allows it to move and create a shaking motion. This motion helps to classify materials as they pass through the screen, enabling small particles to fall through while larger particles are conveyed onward.
Types of Vibrating Screen Mesh
There are several types of vibrating screen mesh available, each suited for different applications and materials
1. Woven Wire Mesh This is the traditional type of screen mesh, made from metal wires woven together. It is durable and can handle high volumes of materials, making it ideal for heavy-duty applications in mining and aggregate processing. Woven wire mesh can be coated with a protective layer to enhance its lifespan and resist corrosion.
2. Perforated Plate Composed of metal plates with uniformly spaced holes, perforated plates offer a rigid alternative to woven mesh. They provide excellent support and are particularly useful for very coarse materials. However, they may have a shorter lifespan compared to wire mesh.
vibrating screen mesh
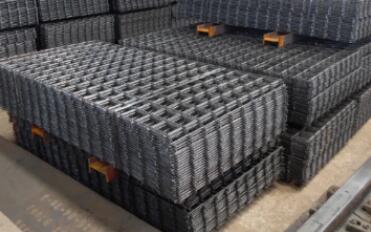
3. Polyurethane Mesh Known for its flexibility and resilience, polyurethane mesh is used in applications requiring high abrasion resistance. It is lighter than metal meshes, making it easier to handle and install. Polyurethane screens are an excellent choice for wet and sticky materials, where traditional wire screens may clog.
4. Self-Cleaning Screens These innovative mesh types feature special designs that prevent material build-up and clogs. They are particularly useful in applications where fine particles are processed because they maintain a consistent screening performance.
Importance of Vibrating Screen Mesh
The effectiveness of a vibrating screen greatly depends on the quality and type of mesh used. A well-chosen screen mesh can significantly enhance the efficiency of material separation, leading to better product quality and reduced operational costs. Here are some critical reasons why vibrating screen mesh is important
- Improved Efficiency The right mesh size allows for optimal flow of materials, ensuring that fines are effectively separated from coarse materials. This increases production rates and improves the overall efficiency of the screening process.
- Material Quality Using the correct mesh type contributes to the production of a more uniform particle size, which is vital for many industrial processes. High-quality separation leads to better end products, whether in construction, pharmaceuticals, or food processing.
- Cost-Effectiveness Investing in durable and efficient screen mesh can reduce maintenance costs over time. Less frequent replacements and repairs lead to lower downtime and higher productivity.
In conclusion, the vibrating screen mesh is an integral component of material separation across various industries. Understanding the different types of mesh available and their respective advantages can help businesses choose the best option for their specific needs, ultimately enhancing efficiency and product quality. As industries evolve and demand for advanced materials processing grows, the importance of high-quality vibrating screen mesh will continue to rise.