Understanding Welded Wire Mesh Types
Welded wire mesh is a versatile material commonly used in construction, agriculture, and various industrial applications. It consists of a grid of wires that are welded together at their intersections, creating a strong and durable mesh. This article explores the different types of welded wire mesh, highlighting their unique characteristics, applications, and benefits.
1. Standard Welded Wire Mesh
The most basic form of welded wire mesh is standard welded wire mesh, which typically comes in sheets or rolls. This type is made from carbon steel wire and is available in various wire gauges and mesh sizes. Standard welded wire mesh is widely used in construction for reinforcing concrete slabs, walls, and foundations. Its grid structure provides excellent tensile strength, making it ideal for supporting heavy loads. Additionally, it can be easily cut and shaped to fit specific project requirements.
2. Galvanized Welded Wire Mesh
Galvanization is a process in which a protective zinc coating is applied to the wire before it is welded. Galvanized welded wire mesh is resistant to corrosion and rust, making it suitable for outdoor applications. This type of mesh is often used in agricultural settings, such as fencing for livestock and poultry enclosures, as well as in landscape applications like garden fencing. Its longevity and durability in harsh weather conditions make it a popular choice for both residential and commercial uses.
3. Stainless Steel Welded Wire Mesh
For applications that require superior corrosion resistance and strength, stainless steel welded wire mesh is the ideal option. Made from high-quality stainless steel wire, this type of mesh is commonly used in food processing, pharmaceutical, and chemical industries where hygiene and durability are critical. Stainless steel welded wire mesh can withstand extreme temperatures and is tolerant of a wide range of chemicals, making it suitable for a variety of demanding environments.
welded wire mesh types
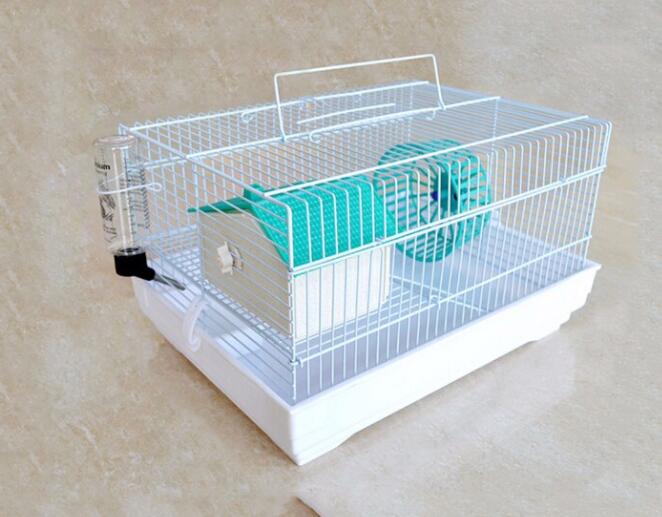
4. Plastic Coated Welded Wire Mesh
Plastic coated welded wire mesh is created by enclosing standard welded wire mesh in a layer of PVC or other plastic. This coating provides additional protection against corrosion and enhances the aesthetic appeal of the mesh, making it a popular choice for decorative fencing and garden enclosures. The colored coating also helps to blend the mesh with its surroundings, adding to its visual compatibility in landscape designs. This type of mesh is generally used in residential areas, parks, and other applications where appearance matters.
5. Expanded Welded Wire Mesh
Unlike the typical welded wire mesh, expanded welded wire mesh is formed from a single sheet of metal that has been cut and stretched to create an opening pattern. This type of mesh is particularly strong and is often used in industrial applications for safety guards, walkways, and platforms. Its open design allows for excellent airflow and visibility, making it suitable for a range of settings, from construction sites to processing facilities.
6. Applications of Welded Wire Mesh
The diverse types of welded wire mesh can be specifically tailored for various applications. In construction, they are used for reinforcement in floors, walls, and roofing systems. In agriculture, they serve as fencing solutions, animal enclosures, and crop support structures. In industrial applications, welded wire mesh can be found in machinery protection, storage racks, and conveyor systems. Additionally, welded wire mesh is also used in artistic and architectural projects, where its unique design can enhance the visual appeal of structures.
Conclusion
In summary, welded wire mesh comes in various types, each offering distinct advantages suited for different applications. From improved corrosion resistance in galvanized and stainless steel options to decorative uses of plastic-coated mesh, the versatility of welded wire mesh is undeniable. Understanding the different types available allows consumers and professionals to select the right mesh for their specific needs, ensuring both functionality and durability in their projects.