The Importance of Wire Mesh Filter Screens in Industry
Wire mesh filter screens play a crucial role in various industrial applications, ranging from water treatment facilities to manufacturing plants. Their primary function is to separate solids from liquids or gases, ensuring the purity and quality of the output. As industries continue to evolve, the demand for efficient filtration systems has surged, making wire mesh filter screens an essential component in modern operations.
Understanding Wire Mesh Filter Screens
Wire mesh filter screens are made from interwoven strands of metal wire that create a finely structured mesh. These screens are available in various materials, including stainless steel, copper, and aluminum, allowing them to withstand a range of operating conditions, including high temperatures and corrosive environments. The mesh's size can be customized, enabling filtration of different particle sizes, ranging from coarse materials to fine particulates.
The manufacturing process of wire mesh involves weaving the wire strands together in a specific pattern, which determines the screen's porosity and strength. Different weaving techniques, such as plain weave, twill weave, and Dutch weave, offer varying strengths and filtration characteristics. This versatility allows industries to select the most suitable wire mesh filter screen for their specific needs.
Applications of Wire Mesh Filter Screens
Wire mesh filter screens are deployed across numerous sectors. In the water treatment industry, they are vital for removing debris, leaves, and larger particles from water sources before further processing. This initial filtration step is crucial for protecting pumps and other equipment from damage and ensuring clean water distribution.
In the food and beverage industry, wire mesh filter screens are used to separate solids from liquids during the production process. For instance, in brewing, these filters help in separating hops and other solids, resulting in a clearer final product. Similarly, in the oil and gas sector, they are utilized to filter impurities from crude oil and natural gas, enhancing the quality of the end products.
wire mesh filter screen
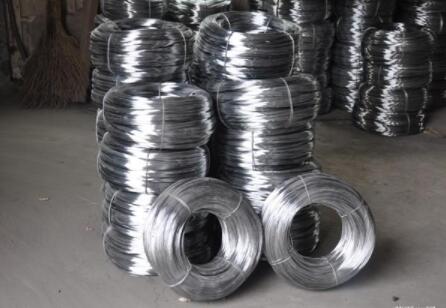
Additionally, wire mesh filter screens are essential in the pharmaceutical industry, where they are used to ensure that production processes remain free from contaminants. The rigorous standards for product purity necessitate the use of high-quality filtration systems.
Advantages of Using Wire Mesh Filter Screens
One of the significant advantages of wire mesh filter screens is their durability. Unlike traditional filters, which may need frequent replacement, wire mesh can be cleaned and reused, making it a cost-effective solution in the long run. This aspect is particularly beneficial in high-volume operations where filtration systems are under constant strain.
Furthermore, wire mesh filter screens can be tailored to meet specific requirements. Industries can customize the material, mesh size, and opening patterns to optimize the filtration process, enhancing efficiency and performance.
Another benefit of wire mesh is its resistance to high temperatures and aggressive chemicals, making it suitable for challenging environments. This resilience ensures longevity and reliability, essential for continuous operation in industrial settings.
Conclusion
In summary, wire mesh filter screens are indispensable in modern industrial applications. Their ability to efficiently separate solids from liquids and gases makes them vital in various fields, including water treatment, food processing, and pharmaceuticals. The durability, customization options, and resistance to harsh conditions further highlight their significance. As industries continue to prioritize efficiency and quality, wire mesh filter screens will remain integral to achieving these goals, ensuring clean and safe operations across diverse sectors.