Understanding Wire Mesh Welding An Overview
Wire mesh welding has emerged as a crucial technique in the construction and manufacturing industries, offering strength, durability, and versatility for a variety of applications. This method involves the fusion of intersecting wires at their junctions through electric resistance, resulting in a grid-like structure that is both lightweight and resilient. In this article, we will explore the intricacies of wire mesh welding, its applications, advantages, and the technology involved in the process.
The Process of Wire Mesh Welding
The wire mesh welding process can be broken down into several key steps. First, the wires, typically made of low-carbon steel or stainless steel, are drawn through machines that stretch and align them into the desired grid format. The wires are then cut to specific lengths based on the mesh requirements.
Next, an automated welding machine applies heat to the intersection points of the wires. This heating occurs due to the electric resistance within the wire, which allows the metal to melt and fuse where it contacts another wire. The result is a solid bond that provides structural integrity to the mesh. After the welding process, the finished wire mesh is cooled, inspected for quality, and then typically coated with a protective layer to ensure longevity and resistance to corrosion.
Applications of Wire Mesh
The applications of wire mesh are vast and varied, reflecting its adaptability. One of the most prominent uses is in construction, where welded wire mesh serves as a reinforcement material in concrete slabs, walls, and other structural elements. The mesh enhances the strength and stability of the concrete, offering support against crack formation under tension and compression loads.
In addition to construction, wire mesh is also utilized in the agricultural sector for fencing and animal enclosures, helping to protect livestock and crops from predators. Architectural designs often incorporate wire mesh for aesthetic features, providing both security and a contemporary look in the form of railings, partitions, and even decorative facades.
wire mesh welding
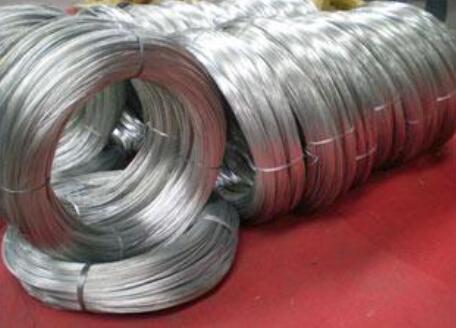
Moreover, wire mesh finds its place in manufacturing industries for filters, screens, and sieves, where it helps in the separation of materials. Its versatility extends to the automotive sector, where it is used in components for air filters and other necessary applications.
Advantages of Wire Mesh Welding
The benefits of wire mesh welding are manifold. One significant advantage is the uniformity of the welds, which ensures consistency in strength throughout the mesh. This precision also leads to reduced material wastage and increased efficiency during the manufacturing process.
Furthermore, wire mesh is lightweight, making it easier to handle and transport. Its adaptability means it can be produced in various sizes, shapes, and wire gauges to meet specific project requirements. The durability of welded wire mesh also cannot be overstated; it withstands harsh environmental conditions, making it suitable for both indoor and outdoor applications.
Technological Advancements
Recent advancements in welding technology have further improved the wire mesh welding process. Automated systems have increased production speeds, while innovations in welding techniques have enhanced the quality of the weld joints. Additionally, the incorporation of robotics in wire mesh welding has allowed for greater precision and the capability to produce complex designs that meet modern architectural demands.
Conclusion
In summary, wire mesh welding plays an indispensable role in multiple sectors, providing a reliable and efficient solution for structural reinforcement and a wide range of other applications. As technology continues to evolve, the future of wire mesh welding appears promising, enabling further enhancements in efficiency, quality, and versatility. Whether in construction, agriculture, or manufacturing, the significance of wire mesh welding in today’s world cannot be overlooked.