Wire Mesh Welding An Overview of Techniques and Applications
Wire mesh welding is a vital manufacturing process that produces sturdy and versatile mesh products widely used across various industries. This technique involves the precise welding of intersecting wire rods to form a grid-like pattern. The resultant wire mesh is characterized by its strength, durability, and adaptability, making it an essential component in construction, infrastructure, agriculture, and many other fields.
The Welding Process
The process of wire mesh welding typically employs automated machinery that enhances precision and efficiency. Two main welding techniques are commonly used spot welding and resistance welding. In spot welding, localized heating is applied at the intersection of wire rods, resulting in a strong bond. Resistance welding involves passing electric current through the wires to generate heat at the joints, melting the wires at their intersection points to form a solid connection.
Both techniques are highly efficient, allowing for rapid production and reduced labor costs. Modern advancements in welding technology have led to the development of automated systems, which can produce large quantities of wire mesh in a relatively short period. The machinery can be programmed to create varying mesh sizes and configurations, catering to the specific needs of different applications.
Applications of Wire Mesh
The versatility of wire mesh makes it suitable for a multitude of applications. One of the most prevalent uses is in the construction industry, where it is utilized as reinforcement in concrete structures. Wire mesh provides added strength and stability to concrete by evenly distributing loads and resisting cracking. This is particularly important in highways, bridges, and buildings, where structural integrity is critical.
In agriculture, wire mesh serves as fencing for livestock enclosures and crop protection. It keeps animals secure while allowing for proper ventilation and light, which is essential for maintaining healthy plants. Additionally, wire mesh is often used in storage applications, such as shelving, cages, and bins, providing support for various items while ensuring visibility and accessibility.
Manufacturers also employ wire mesh in filtration systems. The fine openings in the mesh allow for the effective separation of liquids and solids, making it ideal for applications in water treatment, food processing, and chemical manufacturing. Similarly, wire mesh is employed in the automotive and aerospace industries for safety features and structural components.
wire mesh welding
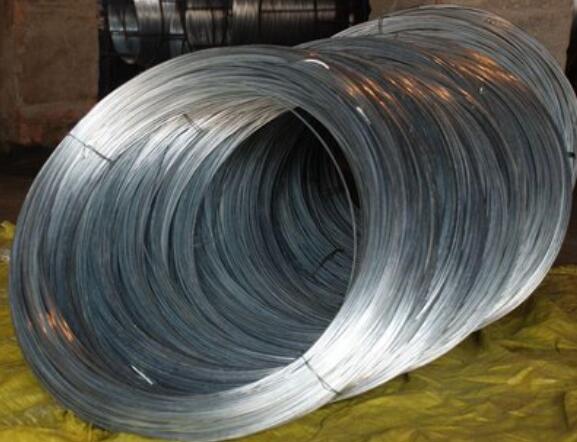
Advantages of Wire Mesh Welding
Wire mesh welding boasts several advantages over alternative manufacturing methods. The most notable benefits include
1. Strength and Durability The welded intersections provide a robust structure capable of withstanding significant stresses and strains.
2. Cost-Effectiveness The automated production process reduces labor costs and increases output, making it a more economical choice for manufacturers.
3. Flexibility Wire mesh can be tailored to specific applications by adjusting the size, spacing, and gauge of the wires.
4. Corrosion Resistance Depending on the material used, wire mesh can be coated or galvanized to resist rust and corrosion, extending its lifespan in harsh environments.
Conclusion
In summary, wire mesh welding is an indispensable process that contributes to the creation of strong, durable, and versatile products used across various sectors. With advancements in technology and an increased focus on efficiency and cost-effectiveness, wire mesh welding is likely to continue evolving, meeting the demands of an ever-changing industrial landscape. As industries grow and innovate, the applications for wire mesh will undoubtedly expand, solidifying its role as a fundamental element in modern manufacturing.