An Overview of Hot Dip Galvanized Wire Manufacturers
Hot dip galvanized wire is an essential material in various industrial applications, renowned for its durability and corrosion resistance. The process of hot dip galvanization involves coating steel wire with a layer of zinc to protect it from rust and deterioration caused by environmental factors. This article will explore the significance of hot dip galvanized wire, the manufacturing process, and the leading manufacturers in the industry.
Importance of Hot Dip Galvanized Wire
Hot dip galvanized wire plays a crucial role across multiple sectors, from construction and agriculture to manufacturing and telecommunications. Its primary advantage lies in its enhanced resistance to corrosion, making it ideal for outdoor applications where exposure to moisture, pollutants, and varying temperatures can lead to rapid deterioration of untreated steel.
In construction, hot dip galvanized wire is often used for reinforcing concrete, creating fences, and providing support structures due to its strength and longevity. In agriculture, it is employed for fencing livestock, trellising, and making cages. The wire's versatility and reliability eventually translate into cost savings, as its longevity reduces the need for frequent replacements.
The Manufacturing Process
The manufacturing of hot dip galvanized wire involves several fundamental steps
1. Wire Drawing This is the initial step where raw steel wire is drawn through a series of dies to achieve the desired diameter. The thickness of the wire can vary based on its intended application.
2. Cleaning Once the wire is drawn, it must be cleaned thoroughly to remove any dirt, oil, or oxidation. This step is critical, as any contamination can prevent proper adhesion of the zinc coating.
3. Pickling The cleaned wire undergoes a pickling process, which involves immersing it in an acid solution. This further removes rust, scale, and oxides, ensuring a clean surface that will accept the zinc coating.
4. Zinc Coating The wire is then dipped into a molten zinc bath at a temperature of around 450°C (842°F). During this process, a metallurgical bond forms between the zinc and the steel, resulting in a robust coating. The thickness of the zinc layer can be controlled by adjusting the speed of the wire through the bath and the duration of immersion.
hot dip galvanized wire manufacturers
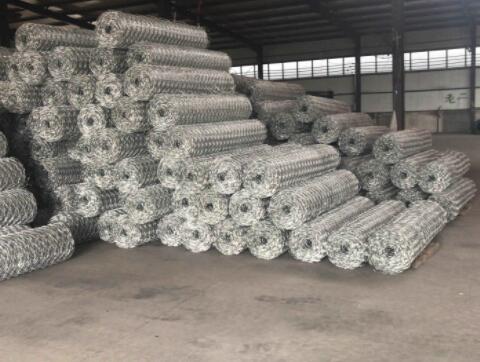
5. Cooling and Inspection After coating, the wire is cooled, often through quenching in water or air to solidify the zinc layer. Finally, the product undergoes rigorous quality checks to ensure it meets industry standards for strength and corrosion resistance.
6. Packaging The galvanized wire is then spooled and packaged for distribution. Proper packaging is important to prevent damage during transportation and storage.
Leading Manufacturers in the Industry
Various manufacturers across the globe specialize in producing hot dip galvanized wire. Some of the most reputable companies include
- WireCo WorldGroup Based in the United States, WireCo is a recognized leader in manufacturing high-quality wire products. They supply a range of galvanized wire suitable for diverse applications, backed by a commitment to sustainability and quality.
- Anhui Guofeng Wire Products Co., Ltd. This Chinese manufacturer is highly regarded for its extensive production capabilities and innovative approaches in wire manufacturing. They export galvanized wire to various international markets.
- Bekaert A global player headquartered in Belgium, Bekaert is known for its extensive research and development efforts, continually improving their products' quality and performance. The company offers a robust portfolio of hot dip galvanized wire for various industries.
- Tianjin Hengxin Metal Products Co., Ltd. With a focus on high-quality galvanized products, this manufacturer has gained recognition for actively addressing the growing demands in construction and agriculture.
Conclusion
Hot dip galvanized wire manufacturers play a vital role in supplying industries with essential materials that promote safety and longevity in various applications. Through an intricate manufacturing process that emphasizes quality and durability, these manufacturers ensure that their products can withstand the rigors of their intended use. As industries continue to grow and evolve, the demand for hot dip galvanized wire is likely to increase, solidifying its importance in the global market.