Understanding the Importance of Wire in Soldering A Comprehensive Guide
Soldering is an essential technique used in electronics, allowing for the joining of metal components and the creation of robust electrical connections. At the heart of this process is solder wire, which plays a pivotal role in ensuring successful soldering results. This article delves into the characteristics, types, and considerations surrounding solder wire, highlighting its importance in achieving reliable solder joints.
What is Solder Wire?
Solder wire is a metal alloy that is melted and used to create a bond between two surfaces, usually metal. When heated, solder wire flows into the joint, filling any gaps and solidifying as it cools, thus forming a strong electrical connection. The most commonly used solder wire consists mainly of tin and lead, although lead-free options have gained popularity due to health and environmental concerns.
Types of Solder Wire
1. Lead-Based Solder Traditionally, solder wire was primarily composed of tin and lead. The most common ratio is 60% tin and 40% lead (60/40 solder). While effective in providing low melting points and excellent flow, lead-based solder poses toxic risks, leading to increased regulation and a shift towards safer alternatives.
2. Lead-Free Solder With the push for environmental sustainability, lead-free solders have emerged as a popular choice. These solder wires often consist of tin, copper, and other metals such as silver or bismuth. Lead-free solder may require higher temperatures to melt and solidify, and it can behave differently compared to lead-based solder during the soldering process.
3. Flux-Cored Solder Wire This type of solder wire incorporates a core of flux, which is a cleaning agent that helps prepare the metal surfaces for soldering. Flux minimizes oxidation and enhances the flow of solder, ensuring a cleaner and stronger joint. When heated, the flux is activated, facilitating the soldering process.
4. Solid Wire In comparison to flux-cored solder, solid solder wire does not contain any flux. It requires the application of separate flux to the joint prior to soldering. This type is often used in specialized applications where more control over the soldering process is needed.
wire for soldering
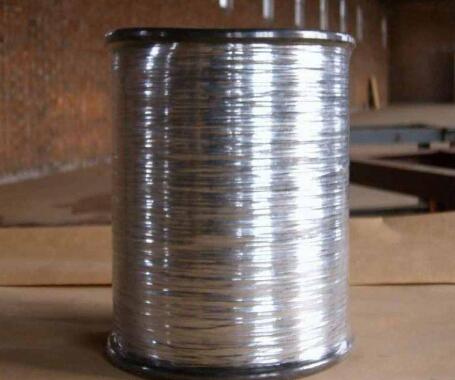
Key Considerations When Choosing Solder Wire
When selecting solder wire for a specific application, several factors should be taken into account
- Melting Point Different solder alloys have varying melting points. It's crucial to choose an alloy that matches the components being soldered and the soldering equipment used.
- Compatibility Ensure that the solder wire is compatible with the metals of the components being joined. For example, certain solder may work well with copper but not with aluminum.
- Diameter Solder wire comes in different diameters, typically ranging from 0.2mm to 1.0mm or even thicker. The chosen diameter should be appropriate for the task at hand. Thinner wire allows for more control, while thicker wire can deliver more solder quickly.
- Flux Type The choice of flux is essential for determining the effectiveness of the solder joint. RMA (rosin mildly activated) and no-clean fluxes are common options, each with its benefits depending on the application.
Conclusion
Understanding the nuances of solder wire is critical for any enthusiast or professional involved in electronics. Whether using lead-based or lead-free solder, selecting the right type of solder wire makes a significant difference in the quality and durability of the solder joints created. By considering factors such as melting point, metal compatibility, diameter, and flux type, one can ensure successful soldering outcomes, ultimately leading to better-performing electronic devices. As technology continues to evolve, the importance of adept soldering techniques and appropriate material selection will remain a cornerstone of reliable electronics manufacturing and repair.