Cold Drawn Wire A Comprehensive Overview
Cold drawn wire is a vital product in the metalworking industry, characterized by its unique properties and diverse applications. This process involves pulling a wire through a die at room temperature, which reduces its diameter while increasing its length. As a result, the wire experiences significant improvements in mechanical properties such as tensile strength, yield strength, and hardness.
The cold drawing process begins with employing a wire rod made of materials like carbon steel, stainless steel, or alloy steel. The wire rod is initially produced through a hot rolling process, which forms it into a larger diameter. Once the rod is cooled, it undergoes cleaning and preparation to eliminate any oxidation or impurities that may affect the quality of the final product.
During the cold drawing operation, the wire is pulled through a series of dies to achieve the desired diameter and surface finish. Each pass through the die reduces the diameter incrementally, while also work-hardening the material. This work-hardening increases the tensile strength of the wire, making it suitable for various demanding applications. After the drawing process, the wire may undergo additional treatments, such as annealing, to relieve internal stresses and improve ductility, depending on the required specifications.
cold drawn wire
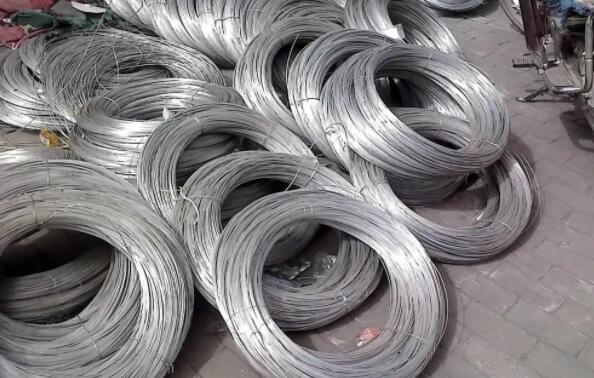
Cold drawn wire is widely used across several industries due to its enhanced mechanical properties. It finds applications in the manufacturing of wire rope, springs, fasteners, and automotive components. The construction industry also benefits from cold drawn wire in the reinforcement of concrete structures, where high-strength materials are essential for ensuring safety and durability.
One of the key advantages of cold drawn wire is its uniformity and precision. The controlled drawing process allows manufacturers to create wire with tight tolerances and consistent characteristics. This level of precision is crucial in applications where the structural integrity of components is paramount. Moreover, the process can produce wire in various shapes, such as round, square, or hexagonal, meeting the specific needs of different applications.
Environmental considerations are also becoming increasingly important in the wire manufacturing industry. Modern cold drawing processes often incorporate energy-efficient practices and recycling initiatives to minimize waste. Additionally, advancements in technology have led to the development of eco-friendly lubricants and cooling agents that reduce the environmental impact during production.
In conclusion, cold drawn wire is an essential component in the metalworking industry, offering exceptional mechanical properties and a wide range of applications. With continuous advancements in manufacturing techniques and a growing emphasis on sustainability, the future of cold drawn wire seems promising. Its ability to meet the evolving demands of various industries, coupled with a focus on quality and environmental responsibility, solidifies its position as a fundamental material in modern engineering and construction. Whether in everyday objects or critical structural components, cold drawn wire plays a pivotal role in ensuring performance and safety across countless applications.