Understanding Steel Sheet Holes Importance, Types, and Applications
Steel sheets are crucial materials in various industries, ranging from construction to manufacturing. One significant aspect of working with steel sheets is the incorporation of holes, which serves numerous functional and aesthetic purposes. This article will explore the importance of holes in steel sheets, the different types, their applications, and best practices in their creation.
The Importance of Holes in Steel Sheets
Holes in steel sheets are essential for several reasons. From a functional perspective, they facilitate the joining of different materials. For instance, in fabrication processes, holes allow for the use of bolts, screws, and rivets that ensure solid connections between structures. Additionally, holes can help reduce the overall weight of a component without sacrificing structural integrity; this is particularly important in industries such as automotive and aerospace, where every gram matters.
Moreover, holes can play a significant role in the thermal and electrical management of steel components. Certain applications require ventilation or the passage of electrical wiring, necessitating holes to provide pathways for these resources. Adequate planning for these features during the design phase can significantly enhance the efficiency and reliability of the final product.
Types of Holes in Steel Sheets
When it comes to the types of holes that can be created in steel sheets, they can be broadly categorized into several classifications
1. Pilot Holes These small-diameter holes serve as starting points for larger hole-making processes, ensuring accuracy when drilling or machining.
2. Through Holes As the name suggests, through holes extend from one side of the sheet to the other. They are commonly used for fastening components together.
3. Blind Holes Unlike through holes, blind holes do not go all the way through the steel sheet. They are often used for applications where internal fastening is required without visible holes on the other side.
4. Countersunk Holes These holes have a conical shape that allows fasteners to sit flush with the surface of the material, providing an aesthetically pleasing finish while reducing the risk of snagging.
steel sheet holes
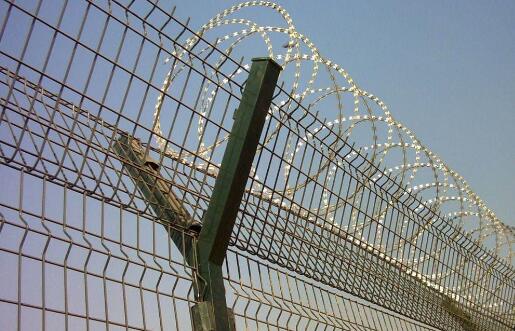
5. Slot Holes These elongated holes provide flexibility for fastening and adjustment purposes. They are often utilized in applications requiring alignment adjustments.
Applications of Holes in Steel Sheets
The applications of holes in steel sheets are vast and varied. In the construction sector, holes are used in beams and columns to facilitate connections between different structural elements. In the automotive industry, manufacturers utilize holes for attaching panels and since vehicles require numerous parts to be securely connected for safety and performance reasons.
Moreover, in aerospace engineering, precision holes are critical for weight management and ensuring that aircraft meet strict safety regulations. Similarly, holes in steel sheets are essential in machinery and equipment, where they facilitate the assembly of mechanical components.
In design and architecture, perforated steel sheets have gained popularity for their aesthetic appeal. These sheets not only provide functional benefits but also contribute to modern design aesthetics, allowing light and air to pass through while maintaining structural soundness.
Best Practices for Creating Holes in Steel Sheets
When creating holes in steel sheets, it’s essential to follow best practices to ensure quality and precision. First, selecting the appropriate tools and techniques is crucial. Common methods for creating holes include drilling, laser cutting, and punching. Each method has its advantages and applications depending on the desired hole size, shape, and finish.
Additionally, proper measurements and alignment before the hole creation process will save time and resources. Using templates or jigs can also enhance accuracy, especially when multiple holes are needed.
Lastly, consideration of the steel sheet’s properties, such as thickness and hardness, is vital to avoid tool wear and ensure precise outcomes. Proper maintenance of tools and regular checks for wear can enhance the longevity of these tools and improve the overall efficiency of the hole-making process.
Conclusion
Holes in steel sheets are far more than mere perforations; they are integral to the functionality, efficiency, and aesthetics of a wide range of products across numerous industries. Understanding the types of holes and their applications is crucial for any engineer or designer in maximizing the potential of steel sheet materials. By adhering to best practices in hole creation, manufacturers can ensure quality and precision in their operations, leading to enhanced product performance and value.