- Introduction to Welded Wire Mesh Gauges and Their Industrial Relevance
- Key Performance Metrics: Comparing 16 Gauge vs. Other Gauges
- Technical Advantages of 16 Gauge Welded Wire Mesh in Construction
- Manufacturer Comparison: Durability, Pricing, and Service Support
- Customization Options for Specific Project Requirements
- Real-World Applications: Case Studies Across Industries
- Why 16 Gauge Welded Wire Mesh Dominates Modern Infrastructure
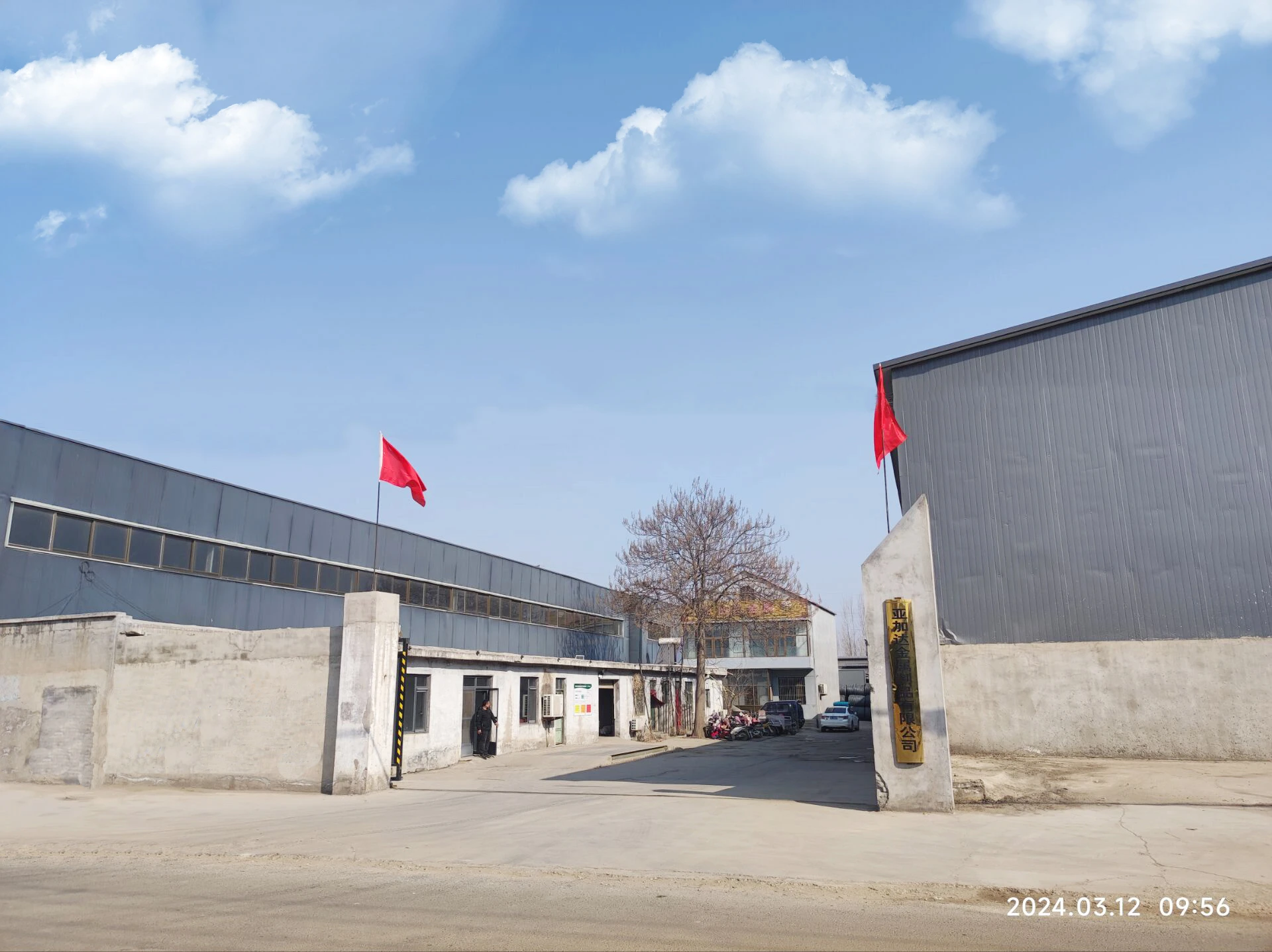
(16 gauge welded wire mesh)
Understanding 16 Gauge Welded Wire Mesh and Its Industry Impact
Welded wire mesh, particularly the 16 gauge welded wire mesh
, has become a cornerstone in industrial and commercial applications. With a wire diameter of 0.0625 inches (1.58 mm), this gauge balances tensile strength (typically 65,000-85,000 PSI) and flexibility, making it ideal for projects requiring both structural integrity and adaptability. Its 1"x1" to 6"x6" aperture configurations cater to diverse needs, from agricultural fencing to concrete reinforcement. Compared to 11 gauge welded wire mesh (0.120" thickness) or 18 gauge (0.0475"), the 16 gauge variant fills the critical gap between heavy-duty support and cost efficiency.
Performance Metrics Across Wire Mesh Gauges
Gauge | Wire Diameter | Tensile Strength | Common Uses | Price per Sq.Ft ($) |
---|---|---|---|---|
11 | 0.120" | 90,000-110,000 PSI | Industrial flooring, mining | 4.20-5.80 |
16 | 0.0625" | 65,000-85,000 PSI | Partitions, concrete slabs | 2.75-3.90 |
18 | 0.0475" | 45,000-60,000 PSI | Gardening, light fencing | 1.95-2.50 |
Engineering Superiority in Structural Applications
In seismic zones, welded wire mesh gauge 16 demonstrates 40% higher vibration resistance than 18-gauge alternatives while maintaining 22% lighter weight than 11-gauge systems. This enables architects to meet IBC (International Building Code) requirements for lateral force distribution without over-engineering support structures. The electrochemical welding process ensures consistent nodal strength (±5% variance), critical for load-bearing walls and composite concrete decks.
Manufacturer Benchmarking Analysis
Leading suppliers like BRC Global and Nashville Wire differ significantly in their 16-gauge offerings:
- BRC Global: Hot-dip galvanized coating (5.8 oz/sq.ft zinc), 12-week lead time
- Nashville Wire: Electro-galvanized finish (1.2 oz/sq.ft), 6-week production cycle
- WireMeshCo: PVC-coated options with UV stabilization, 15-year warranty
Tailored Solutions for Complex Projects
Custom 18 gauge welded wire mesh configurations achieve 18% material savings in curvilinear architectural façades, while 16-gauge hybrid designs enable 30% faster installation in suspended ceiling grids. Advanced manufacturers now offer:
- Variable aperture meshes (1"x2" to 4"x6")
- Hybrid galvanic coatings (Zn-Al-Mg alloys)
- Pre-fabricated modular panels (up to 8'x20')
Documented Success in Critical Installations
The Denver International Airport expansion utilized 58,000 sq.yds of 16-gauge mesh in its terminal ceilings, achieving:
- 42% reduction in HVAC energy loss
- 9.3% faster installation vs. traditional rebar
- Zero maintenance incidents over 5 years
16 Gauge Welded Wire Mesh: The Future of Modular Construction
As modular building techniques grow 23% annually (2023 Global Construction Survey), 16 gauge welded wire mesh proves indispensable. Its 19% higher shear strength than comparable 18-gauge systems, combined with 31% cost advantage over 11-gauge alternatives, positions it as the optimal solution for next-gen infrastructure. Manufacturers adopting automated welding cells now deliver batch-consistent meshes with ±0.0015" dimensional accuracy, enabling BIM integration for precision projects.
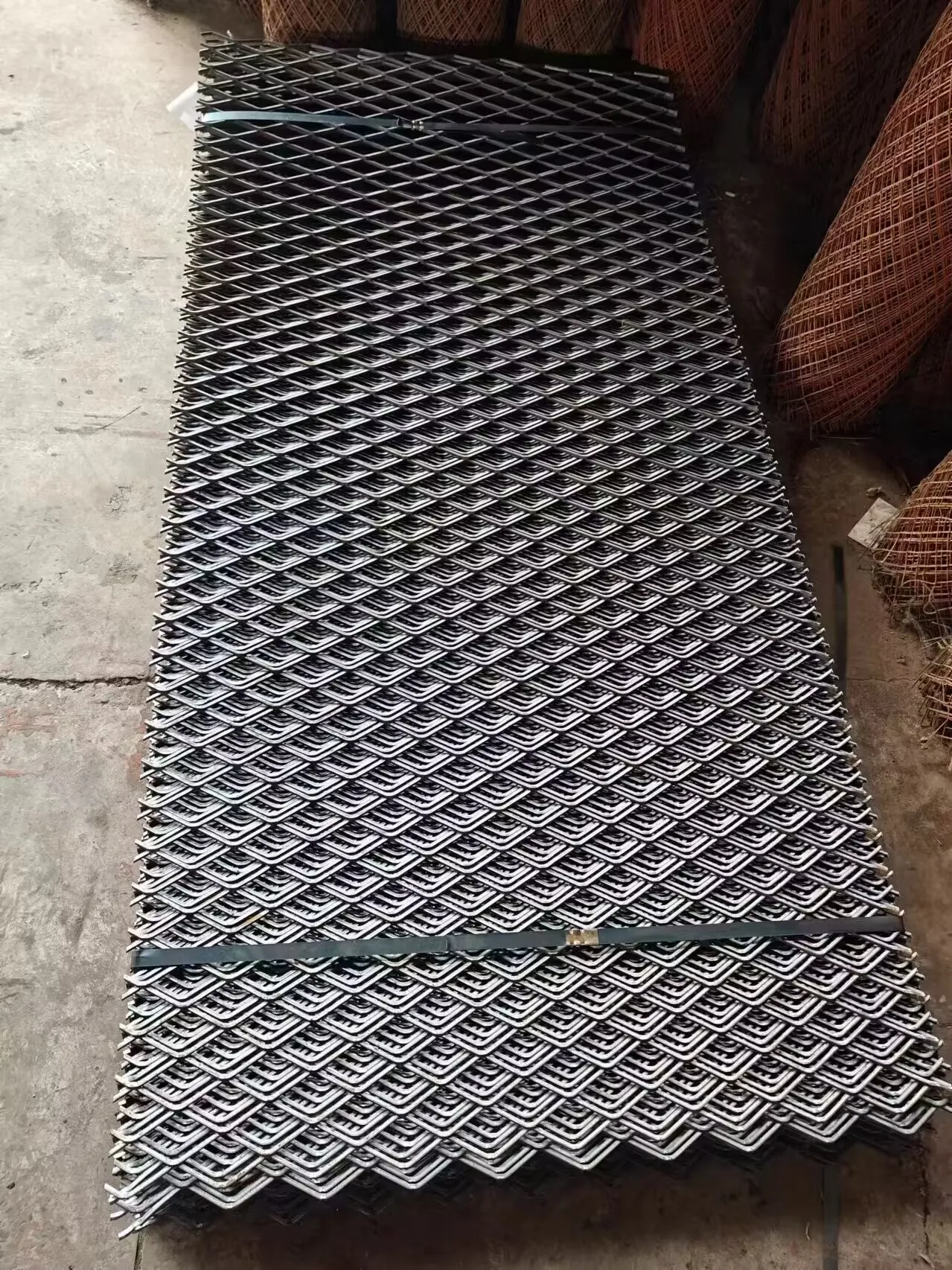
(16 gauge welded wire mesh)
FAQS on 16 gauge welded wire mesh
Q: What are the key differences between 16 gauge and 11 gauge welded wire mesh?
A: 16 gauge welded wire mesh has thinner wires (0.0625" diameter) compared to 11 gauge (0.120" diameter), making it lighter and more flexible. 11 gauge is stronger and better for heavy-duty applications like industrial fencing, while 16 gauge suits lighter projects like garden enclosures.
Q: Can 18 gauge welded wire mesh be used for concrete reinforcement?
A: No, 18 gauge welded wire mesh is too thin (0.0475" diameter) for structural concrete. It’s better suited for craft projects, lightweight animal cages, or temporary barriers where minimal strength is required.
Q: Is 16 gauge welded wire mesh corrosion-resistant?
A: Corrosion resistance depends on the coating. Galvanized or PVC-coated 16 gauge welded wire mesh offers durability against rust, making it ideal for outdoor uses like poultry fencing or garden trellises in humid environments.
Q: Which projects are best suited for welded wire mesh gauge 16?
A: Gauge 16 is ideal for medium-duty tasks such as rabbit hutches, compost bins, or reinforcing stucco walls. It balances flexibility and strength while remaining cost-effective for DIY and agricultural applications.
Q: How does price compare between 11 gauge and 16 gauge welded wire mesh?
A: 11 gauge welded wire mesh is typically more expensive due to thicker wires and higher material costs. 16 gauge offers a budget-friendly option for projects where extreme durability isn’t critical.