Understanding 5% Mesh Screen An Essential Tool in Filtration and Separation
The concept of a mesh screen is integral to various industries, ranging from food processing to water treatment and even in manufacturing. A 5% mesh screen is often discussed within the context of filtration, separation, and sieving processes. This article aims to provide a comprehensive overview of a 5% mesh screen, its applications, benefits, and some key considerations when selecting the right mesh for specific needs.
What is a Mesh Screen?
A mesh screen consists of a network of wires or fibers arranged in a specific pattern, creating openings or “pores” between them. The size of these openings determines the screen’s ability to filter or separate materials. The term “5% mesh screen” typically refers to a screen where 5% of the total area is made up of openings, while the remaining 95% is composed of solid material. This low percentage indicates that the screen is primarily designed to retain larger particles while allowing fine materials to pass through.
Applications of 5% Mesh Screens
1. Filtration Systems One of the primary uses of a 5% mesh screen is in filtration systems where the goal is to remove larger debris from fluids. For example, in water treatment facilities, these screens can prevent sand, leaves, and other large contaminants from entering pumps and pipelines.
2. Food Industry In food processing, maintaining hygiene and quality is crucial. 5% mesh screens can be employed in various applications, such as separating pulp from juice or ensuring that spices are free from larger impurities during the grinding process.
3. Mining and Minerals In mineral processing, mesh screens play a critical role in classifying materials. A 5% mesh screen can be utilized to separate larger shards from finer minerals, thereby optimizing the recovery process.
4. Chemical Processing In the chemical industry, these screens are essential in maintaining the purity of chemical products by filtering out larger particles that may interfere with the end product.
Benefits of Using a 5% Mesh Screen
- Efficiency in Separation A 5% mesh screen is designed for high efficiency, allowing smaller particles to pass through while effectively holding back larger materials. This capability is critical in maintaining the quality of the final output in various processes.
5 mesh screen
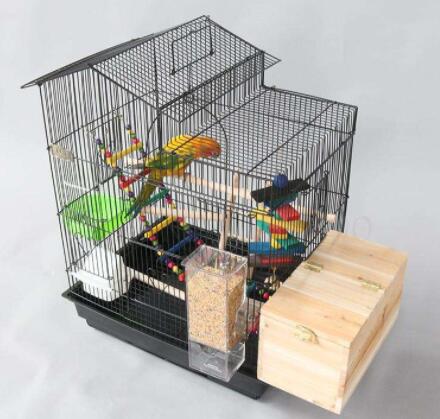
- Durability Mesh screens are often made from robust materials such as stainless steel, allowing them to withstand harsh environments and chemical exposure, thereby increasing their lifespan and reliability.
- Cost-Effective By efficiently filtering out larger materials, a 5% mesh screen can help reduce wear and tear on pumps and machinery, leading to lower maintenance costs and increased operational uptime.
- Customizability Many manufacturers offer custom mesh sizes and configurations, allowing businesses to tailor the screens to their specific operational needs.
Key Considerations When Choosing a 5% Mesh Screen
When selecting a 5% mesh screen, several factors must be taken into account
1. Material Composition Depending on the application, the material of the mesh screen should be resistant to corrosion and wear. Stainless steel is often preferred for its durability, especially in food and chemical applications.
2. Mesh Size The size of the mesh openings should align with the specific filtration needs of the application. Even within the category of 5% screens, variations in mesh size can significantly impact performance.
3. Flow Rate It is essential to consider the flow rate of the material being filtered. A screen that is too fine may restrict flow, while one that is too coarse may allow undesirable particles to pass through.
4. Cleaning and Maintenance The ease of cleaning the mesh screen should also be considered, as this can affect operational efficiency and the longevity of the screen.
In conclusion, a 5% mesh screen is a vital tool in various industries that require efficient filtration and separation. Understanding its applications, benefits, and relevant selection criteria can help businesses optimize their processes, enhance product quality, and improve operational efficiency. Whether in food processing, chemical manufacturing, or water treatment, the right mesh screen can make a significant difference in performance and productivity.