The Manufacturing Process of Iron Nails
Iron nails have been essential components in construction and various woodworking applications for centuries. Their reliability and strength make them a staple in both industrial and artisanal contexts. The manufacturing of iron nails, while straightforward, involves a series of carefully controlled steps to ensure quality and performance. This article explores the intricate process of iron nail manufacturing, from raw material selection to the final product.
Raw Material Selection
The first step in the production of iron nails is the selection of high-quality raw materials. The primary ingredient is iron, which is often obtained from iron ore. The ore undergoes smelting to separate metallic iron from impurities and other minerals. During this process, additional alloying elements may be introduced to enhance specific properties of the iron, such as strength, ductility, and corrosion resistance.
Melting and Forming
Once the iron is sourced, the next step is melting. The molten iron is produced in a blast furnace, where the ore, coke, and limestone are heated at high temperatures. The heat facilitates the reduction of iron, resulting in molten iron that is then cast into desired forms.
For nail manufacturing, iron is typically shaped into wire through processes known as wire drawing. This involves pulling the molten iron through a series of dies of decreasing diameter to create long, thin rods. These rods are then coiled for easy handling and transport to the next manufacturing phase.
Cutting and Shaping
When the wire arrives at the nail manufacturing facility, it undergoes the cutting and shaping process. The wire is fed through a nail machine, which automatically cuts it into predetermined lengths based on the required nail size. The cut pieces are then shaped with the help of dedicated machinery to form the head and point of the nails.
This process can vary slightly depending on the type of nail being produced. For instance, common nails, which have a flat head and sharp point, are formed differently compared to finishing nails, which are designed to be driven deeper into the material, leaving a small hole on the surface.
iron nail manufacturing
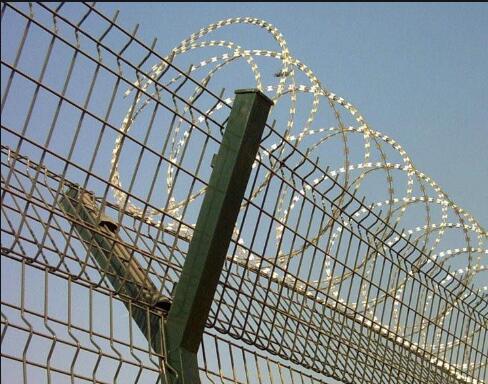
Heat Treatment
After the nails have been shaped, they undergo heat treatment to enhance their physical properties. Heat treatment typically involves heating the nails to high temperatures and then cooling them rapidly (quenching). This process alters the microstructure of the iron, resulting in improved hardness and durability.
The heat treatment process is crucial, as it affects the overall strength and resistance of the nails to bending and breaking during application. Some manufacturers may also apply additional treatments or coatings to further enhance the nails' performance, particularly in outdoor applications where rust resistance is critical.
Surface Finishing
The final phase of the manufacturing process is surface finishing. This can involve various techniques including polishing, galvanizing, or applying protective coatings to ensure the nails are resistant to corrosion and wear. Galvanization, for example, involves coating the nails with a layer of zinc to protect against environmental factors.
Surface finishing not only enhances the durability of the nails but also improves their aesthetic appeal. Some manufacturers choose to produce nails with black oxide or other color finishes that cater to specific market needs.
Quality Control
To ensure that only the highest quality nails reach the market, rigorous quality control measures are implemented throughout the manufacturing process. Each batch of nails is tested for strength, consistency, and adherence to industry standards. Manufacturers must comply with regulations and specifications set by relevant authorities, ensuring that their products are safe for consumer use.
Conclusion
In summary, the manufacturing process of iron nails is a complex yet efficient operation that transforms raw materials into one of the most widely used construction components. From careful selection of iron to precise cutting, shaping, and finishing, each step plays a crucial role in ensuring the quality and performance of the final product. As technology advances, the nail manufacturing industry continues to innovate, exploring new materials and methods to meet the evolving needs of consumers and builders alike. Whether for construction, art, or craft, iron nails remain an indispensable tool in various applications around the world.