Welding Perforated Sheet Techniques, Applications, and Considerations
Perforated sheets are metal panels that have been stamped or punched with a series of holes that can vary in size, shape, and pattern. They are widely used in various industries, including architecture, automotive, and manufacturing. The welding of perforated sheets presents unique challenges and opportunities due to their distinct properties and applications. This article delves into the techniques, applications, and considerations involved in welding perforated sheets.
Understanding Perforated Sheets
Perforated sheets are characterized by their lightweight yet strong structure, making them an appealing choice for various applications. The holes can serve numerous functions, including providing ventilation, reducing weight, or creating a decorative appearance. Depending on the intended use, perforated sheets can be made from different materials such as stainless steel, aluminum, and carbon steel. Each material has its unique welding characteristics, which play a crucial role in the welding process.
Welding Techniques for Perforated Sheets
Welding perforated sheets requires specific techniques to ensure strong joints without compromising the integrity of the material. Here are a few common welding methods used for perforated sheets
1. TIG Welding (Tungsten Inert Gas) The TIG welding process is highly regarded for its precision and control. It uses a non-consumable tungsten electrode to produce the weld and an inert gas to shield the weld area from contamination. TIG welding is ideal for perforated sheets, particularly for stainless steel, as it generates minimal heat and reduces the risk of warping or damaging the material.
2. MIG Welding (Metal Inert Gas) MIG welding is another popular choice for welding perforated sheets. It employs a continuous wire feed and an inert gas mixture to protect the weld area. MIG welding is generally faster than TIG and works well for thicker materials. However, it may introduce more heat, which can lead to distortion in delicate perforated sheets.
3. Spot Welding Spot welding is a method that is particularly beneficial for joining perforated sheets in applications where a quick and efficient joining method is needed. It involves applying heat and pressure to specific points on the material, resulting in strong joints without running the risk of excessive heat affecting the entire sheet.
4. Laser Welding Laser welding is an advanced technique that provides high precision and minimal thermal distortion. This method utilizes a laser beam to melt the metal, producing very small and clean welds. It's particularly effective for thin perforated sheets, where maintaining the sheet's integrity is crucial.
Applications of Welded Perforated Sheets
welding perforated sheet
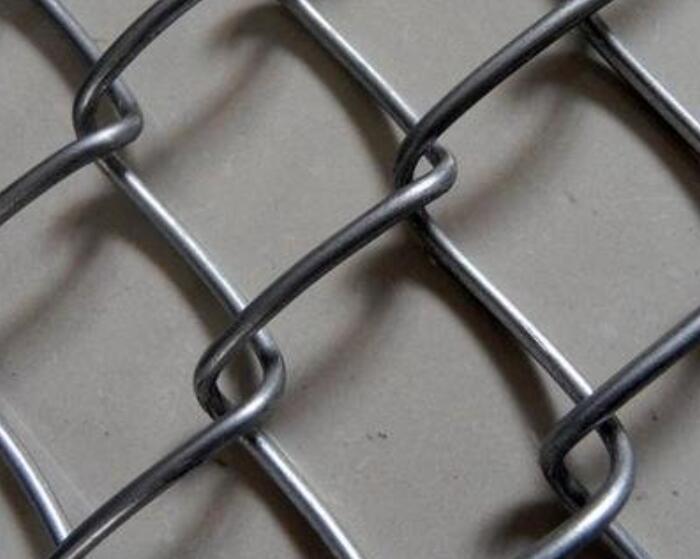
Welded perforated sheets have diverse applications across various industries. Here are a few prominent uses
- Architectural Designs Perforated sheets are popular in architecture for both functional and aesthetic purposes. They can be used as facades, sunshades, and decorative elements. When welded, these sheets maintain their structural stability while offering a unique visual appeal.
- Industrial Filtration In manufacturing and processing industries, welded perforated sheets are often employed in filtration systems. The arrangement of holes allows for efficient fluid flow while capturing unwanted particles, contributing to a cleaner process.
- Automotive Applications The automotive industry also utilizes welded perforated sheets in areas like exhaust systems and heat shields. The lightweight nature of these sheets helps reduce the overall vehicle weight, thus improving fuel efficiency.
Considerations in Welding Perforated Sheets
When welding perforated sheets, several factors must be taken into account to ensure successful outcomes
- Material Thickness Consider the thickness of the perforated sheet, as thicker materials may require different welding settings compared to thinner ones.
- Heat Management Maintaining appropriate heat settings is vital to prevent warping or burning through the perforated material. Utilizing heat sinks or preheating methods can be beneficial.
- Joint Design The design of the joint plays a crucial role in the overall strength and functionality of the welded perforated sheets. Proper alignment and fitting are necessary to achieve optimal results.
In conclusion, welding perforated sheets is a specialized process that combines diverse techniques tailored to specific material properties and applications. As industries continue to evolve and demand innovative solutions, the welding of perforated sheets will remain a key component in advancing manufacturing and design practices. Understanding the techniques, applications, and considerations involved can lead to more effective and efficient welding outcomes.