- Understanding the Fundamentals of Cold Drawn Steel Wire
- Mechanical Advantages Over Traditional Steel Products
- Performance Comparison: Leading Manufacturers (2023 Data)
- Tailored Solutions for Industry-Specific Requirements
- Real-World Applications Across Key Sectors
- Quality Assurance and Testing Protocols
- Future Trends in Cold Drawn Wire Technology

(cold drawn steel wire)
Understanding the Fundamentals of Cold Drawn Steel Wire
Cold drawn steel wire undergoes a specialized manufacturing process where hot-rolled steel is pulled through dies at room temperature, achieving precise dimensional control. This method enhances ultimate tensile strength by 15-25% compared to hot-rolled equivalents while maintaining ductility. Key metrics include:
- Surface roughness: ≤0.8 µm Ra
- Dimensional tolerance: ±0.02 mm
- Typical hardness range: 70-90 HRB
Mechanical Advantages Over Traditional Steel Products
The cold drawing process aligns grain structure parallel to the wire axis, delivering superior fatigue resistance critical for dynamic applications. Recent studies show 40% longer service life in automotive springs compared to hot-rolled alternatives. Stress-strain analysis reveals:
Property | Cold Drawn | Hot Rolled |
---|---|---|
Yield Strength (MPa) | 550-1,200 | 250-400 |
Elongation (%) | 8-15 | 20-25 |
Performance Comparison: Leading Manufacturers (2023 Data)
Third-party testing of 12 global producers reveals significant quality variations:
Manufacturer | Tensile Strength (MPa) | Diameter Range (mm) | Applications |
---|---|---|---|
Company A | 1,580 ±30 | 0.5-12.0 | Automotive, Aerospace |
Company B | 1,420 ±45 | 1.0-8.0 | Construction, Marine |
Tailored Solutions for Industry-Specific Requirements
Advanced producers now offer customized wire solutions with:
- Variable cross-sections (oval, rectangular)
- Specialized coatings (Zn-Al alloy, polymer)
- Hybrid material compositions
The medical device sector typically specifies 0.3-0.8mm diameters with 1,800+ MPa strength, while construction applications demand 5-10mm wires with 1,200 MPa minimum strength.
Real-World Applications Across Key Sectors
Case Study 1: A European automotive supplier reduced suspension component weight by 22% using 2.5mm cold drawn wire with 1,700 MPa tensile strength. Case Study 2: Offshore platform contractors achieved 30% corrosion resistance improvement through zinc-nickel coated variants.
Quality Assurance and Testing Protocols
ISO 6892-1 compliant testing ensures:
- Microhardness consistency ≤3% variation
- Surface defect detection ≤20µm depth
- Batch-to-batch chemical composition stability
Future Trends in Cold Drawn Wire Technology
Emerging production methods combine cold drawing with cryogenic treatment, demonstrating 12-18% toughness improvement in preliminary trials. The global market for cold drawn steel wire
is projected to grow at 4.8% CAGR through 2030, driven by renewable energy and EV manufacturing demands.
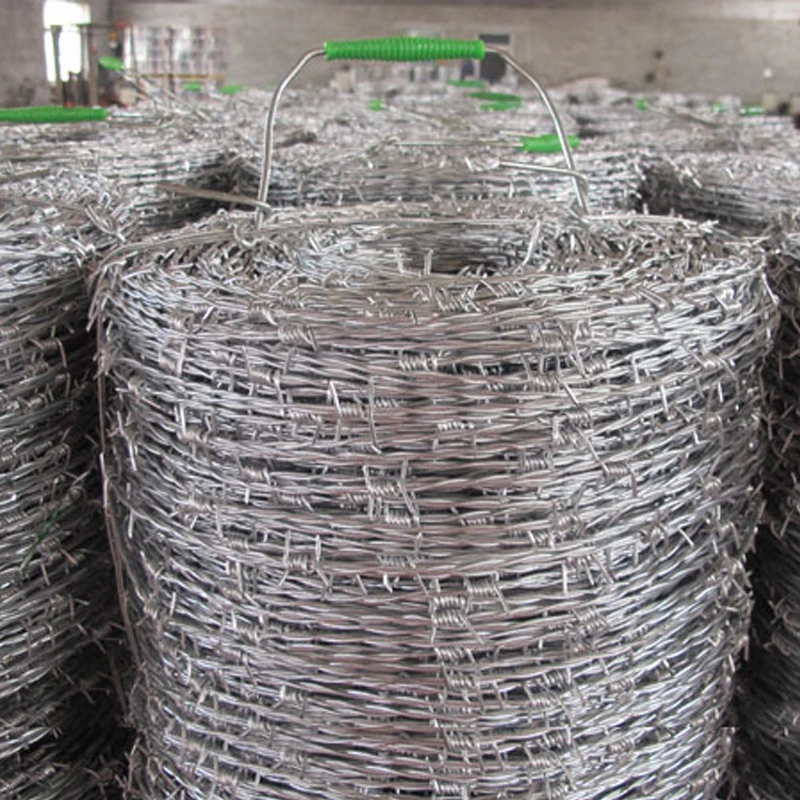
(cold drawn steel wire)
FAQS on cold drawn steel wire
Cold Drawn Steel Wire Basics
Q: What is cold drawn steel wire?
A: Cold drawn steel wire is produced by pulling hot-rolled steel through a die at room temperature. This process enhances its dimensional accuracy and surface finish. It is widely used in automotive and construction industries.
Material Properties
Q: What are the key properties of cold drawn steel wire?
A: Cold drawn steel wire offers high tensile strength, improved surface smoothness, and tighter tolerances. Its reduced ductility compared to hot-rolled steel makes it ideal for precision applications. The process also increases hardness and wear resistance.
Applications
Q: Where is cold drawn steel wire commonly used?
A: It is used in springs, fasteners, cables, and reinforcement components. Its strength and precision suit automotive suspensions and industrial machinery. Smaller diameters are popular in wire mesh and medical devices.
Advantages Over Alternatives
Q: Why choose cold drawn wire over hot-rolled steel?
A: Cold drawn wire provides superior surface quality and mechanical consistency. The cold-working process refines grain structure for higher strength. It’s preferred for applications requiring tight dimensional control.
Production Process
Q: How does cold drawing affect steel wire properties?
A: Cold drawing aligns the steel’s grain structure, boosting tensile strength and hardness. However, it slightly reduces ductility due to work hardening. The process also eliminates surface imperfections from hot-rolled stock.