Understanding Cold Drawn Steel Wire Properties, Applications, and Production Process
Cold drawn steel wire is an essential material in various industrial applications, known for its superior strength and precision. The process of cold drawing involves pulling a rod or wire through a series of dies to reduce its diameter and increase its length, all while maintaining room temperature. This results in a product that exhibits improved mechanical properties and surface finish compared to its hot-rolled counterpart.
One of the primary advantages of cold drawn steel wire is its enhanced tensile strength. The cold working process that the wire undergoes induces dislocation movements in the crystal structure of the metal. This results in strain hardening, allowing the wire to withstand greater loads without deformation. In practical terms, cold drawn steel wire can have tensile strengths that meet or exceed 1,000 MPa, making it suitable for demanding applications.
Moreover, cold drawn steel wire has a much finer surface finish than hot-rolled wire. The drawing process does not only change the geometry of the wire but also creates a smoother outer surface, which is crucial in applications that require precise fitment and reduced friction. This surface quality can also improve the wire's corrosion resistance when appropriately treated or coated.
The applications of cold drawn steel wire are broad and varied. It is widely used in the automotive industry for producing components such as springs, wire harnesses, and many structural elements. The construction sector also relies heavily on cold drawn wire, employing it in the fabrication of reinforcing mesh and other structural reinforcements. Additionally, the material is favored in the production of various wire products, including nails, fasteners, and fencing.
cold drawn steel wire
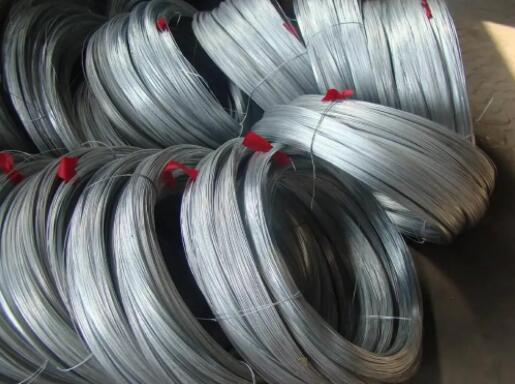
In the electronics and telecommunications industry, cold drawn steel wire is often used in the manufacturing of connectors and cable, due to its excellent conductivity when alloyed properly, as well as its mechanical strength. Other unique applications include the production of medical devices and equipment, where precision and reliability are paramount.
The production process of cold drawn steel wire starts with hot rolled steel rods, which are first inspected for quality. Any rods that meet the necessary specifications are then cleaned to remove any surface oxides or oils. Following this, the rods are drawn through a series of progressively smaller dies. Each pass through a die reduces the wire's diameter while increasing its length.
To further enhance its characteristics, cold drawn steel wire may undergo various treatments. Annealing, for instance, is often employed after the drawing process to relieve internal stresses and restore ductility. This step is crucial for applications that demand further forming. Additionally, coatings may be applied to improve corrosion resistance or electrical conductivity, depending on the end-use.
In conclusion, cold drawn steel wire is a vital component in many modern industries, characterized by its remarkable strength and versatility. Its unique properties make it suitable for a plethora of applications, from automotive to electronics. Understanding the production process and the multitude of benefits this type of wire offers can help industries make informed decisions about material selection, ultimately leading to enhanced performance and durability of products. As technology advances, the demand for high-quality cold drawn steel wire will likely continue to grow, supporting innovations in countless fields.