The Iron Nails Factory A Cornerstone of Industry
In the world of manufacturing, iron nails may seem like a simple product, yet they play a crucial role in construction and various other applications. The iron nails factory stands as a testament to industrial ingenuity, showcasing the blend of traditional craftsmanship and modern technology that has evolved over centuries. This article delves into the operations of an iron nails factory, exploring its significance in both the economy and everyday life.
The manufacturing process of iron nails begins with high-quality iron or steel wire. Factories typically source raw materials from reputable suppliers to ensure durability and strength. The wire is then unwound and cut into precise lengths, which form the basis for the nails. This initial step is critical, as the dimensions directly influence the nail’s performance in various applications, from woodworking to heavy construction.
Once cut, the wire undergoes a process known as heading, where the nail heads are formed. This is accomplished using a specialized machine that strikes the wire ends, creating sturdy heads that facilitate easy driving into materials. The efficiency of this process is impressive, with machines capable of producing thousands of nails per hour, showcasing the power of automation in modern manufacturing.
iron nails factory
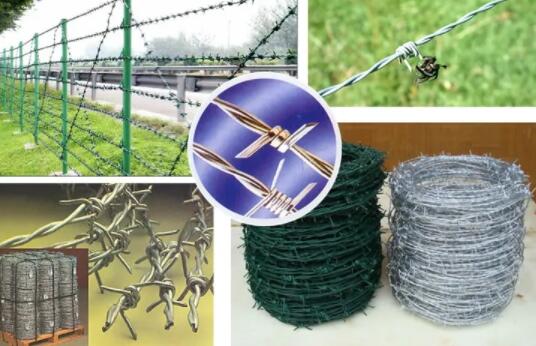
After heading, the nails are sharpened and sometimes coated to prevent rust and enhance durability. The coating process can involve galvanization, which adds a layer of zinc to the surface, significantly extending the lifespan of the nails in outdoor and humid environments. Quality control is an essential aspect of the factory's operations; every batch undergoes thorough inspection to ensure the nails meet industry standards and specifications.
Beyond the manufacturing process, the iron nails factory plays a vital role in the economy. By providing essential materials for construction projects, it supports countless industries, from residential building to infrastructure development. The demand for nails is constant, driven by both new construction and renovation projects, making this factory a significant contributor to local and national economies.
Moreover, an iron nails factory often embodies sustainable practices. Many modern facilities focus on minimizing waste and employing eco-friendly technologies. By recycling scrap metal and utilizing energy-efficient machinery, these factories not only reduce their carbon footprint but also lower operational costs, creating a win-win scenario for both business and the environment.
In conclusion, the iron nails factory is much more than just a production facility; it is a critical part of the supply chain that sustains the construction industry. Through innovative manufacturing techniques and a commitment to quality, these factories ensure that the humble iron nail remains a vital component in building our world. As technology continues to advance, the future of iron nails manufacturing looks promising, paving the way for even more efficient and sustainable practices.