- Introduction to 15 Coil Nails: Versatility and Structural Importance
- Technical Advantages: Precision Manufacturing & Material Composition
- Manufacturer Comparison: 15 Coil Nails, 1 3 4 Coil Siding Nails, 1 1 2 Coil Siding Nails, 3 1 2 Coil Framing Nails
- Customization Options for Project-Specific Requirements
- Application Case Studies: Real-World Performance Insights
- Market Trends: Growth Statistics and Industry Demands
- Conclusion: Why 15 Coil Nails Remain a Leading Choice
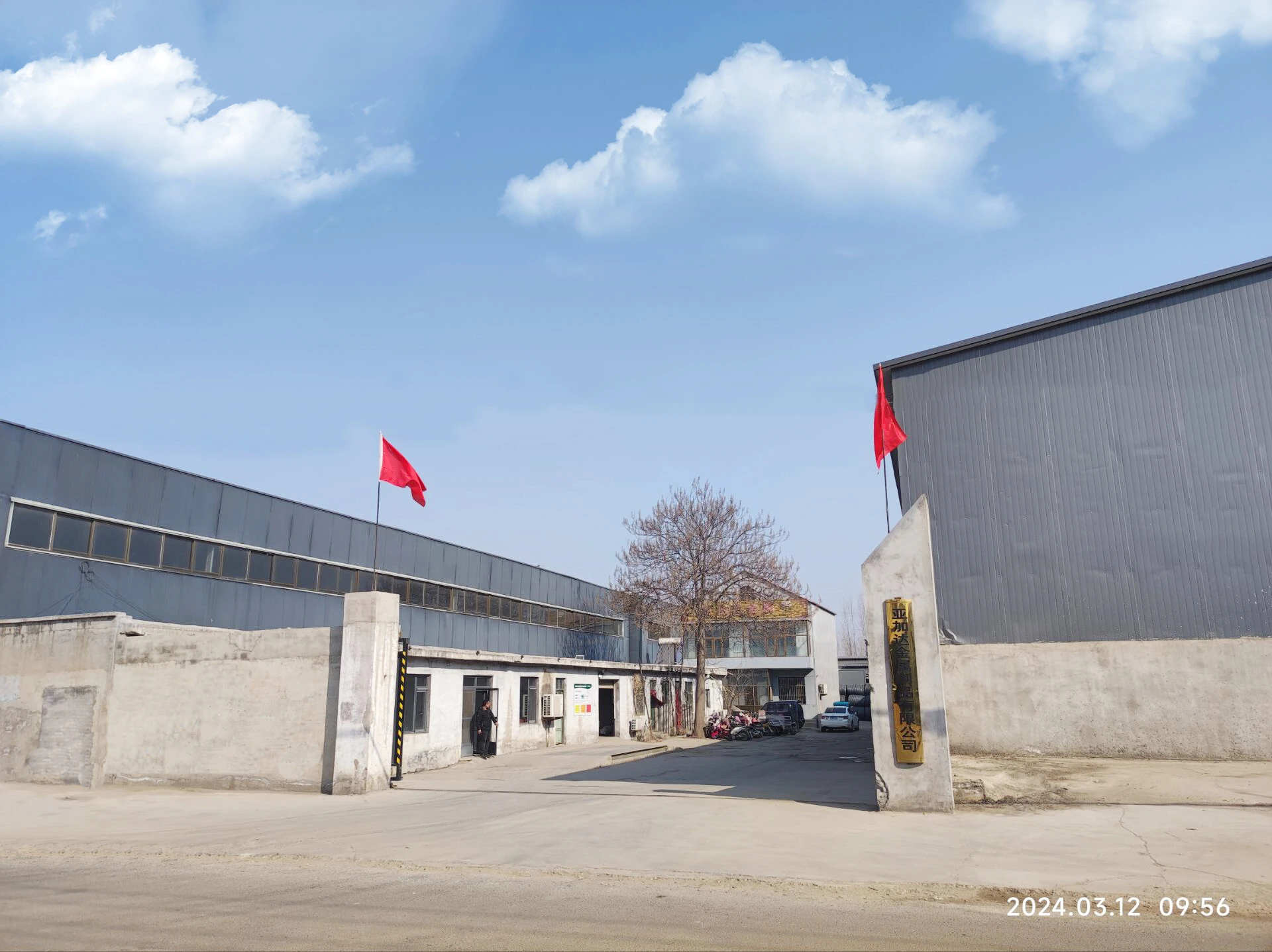
(15 coil nails)
Introduction to 15 Coil Nails: Versatility and Structural Importance
The 15 coil nails
have become a cornerstone in construction and manufacturing industries due to their adaptable applications in both light and heavy-duty projects. Designed for pneumatic and automated nailers, these nails streamline workflow, bolstering productivity and structural integrity. Contractors and builders prefer coil nails for high-load tasks, framing, siding, and wooden assembly jobs. The range encompasses not just the standard 15 coil nails, but also related specifications such as 1 3 4 coil siding nails, 1 1 2 coil siding nails, and 3 1 2 coil framing nails, each tailored for targeted use cases. Their high holding power, resistance to pullout, and ease of handling make them indispensable in ensuring safety, compliance, and aesthetic finish in construction.
Whether used for exterior siding, decking, pallet assembly, or structural framing, these nails support accelerated timelines while reducing operational costs. As demand for durable and versatile fastening solutions climbs, 15 coil nails and their companions stand out for their adaptability across diverse substrates and project scales.
Technical Advantages: Precision Manufacturing & Material Composition
The performance of 15 coil nails rests heavily on precise manufacturing processes and advanced metallurgy. Made predominantly from high-grade steel, these nails undergo stringent quality controls, ensuring uniform diameter, consistent collation, and impeccable point geometry. Heat treatment or galvanization processes enhance corrosion resistance, a critical feature for exterior and moisture-prone environments. Compared with traditional loose and strip nails, the collated arrangement in coils supports seamless feeding, reducing tool jamming and reloading frequency.
For instance, 1 3 4 coil siding nails and 1 1 2 coil siding nails are often treated with specialized coatings to maximize outdoor endurance and adhesion within siding panels. Comparative penetration tests show that coil framing nails like the 3 1 2 coil framing nails can achieve up to 38% greater holding power than similarly sized strip nails. These technical refinements directly translate to fewer callbacks, improved onsite efficiencies, and an extended service life for finished assemblies.
Manufacturer Comparison: Coil Nail Grades & Standards
Choosing the right coil nail resting not only on specifications but also on supplier competence and material traceability. Leading manufacturers invest in state-of-the-art machinery, ensure ISO-certifications, and offer a spectrum of sizes, coatings, and shank profiles. Below is a comprehensive table illustrating key differences between top-brand offerings for 15 coil nails, 1 3 4 coil siding nails, 1 1 2 coil siding nails, and 3 1 2 coil framing nails:
Specification | Brand A | Brand B | Brand C |
---|---|---|---|
15 Coil Nails (Length/Dia.) |
2.5" × 0.092" | 2.5" × 0.099" | 2.5" × 0.090" |
Collation Type | Wire | Plastic | Wire |
Coating | Hot-dip Galvanized | Vinyl Coated | Bright |
Yield Strength (MPa) | 1200 | 1100 | 1180 |
1 3 4 Coil Siding Nails (Length/Dia.) |
1.75" × 0.083" | 1.75" × 0.090" | 1.75" × 0.086" |
Tip Style | Chisel | Blunt | Diamond |
1 1 2 Coil Siding Nails (Length/Dia.) |
1.5" × 0.083" | 1.5" × 0.090" | 1.5" × 0.086" |
Shank Type | Smooth | Ring | Screw |
3 1 2 Coil Framing Nails (Length/Dia.) |
3.5" × 0.131" | 3.5" × 0.120" | 3.5" × 0.131" |
Pulout Resistance (lbs) | 710 | 670 | 695 |
Corrosion Warranty | 15 Years | 10 Years | 12 Years |
This comparison shows that technical advancements, such as diversified shank designs and robust coatings, significantly influence nail performance and durability. It also demonstrates the premium placed on yield strength, ease of penetration, and long-term corrosion resistance across brands.
Customization Options for Project-Specific Requirements
Not all projects conform to standard specifications. Various industries—be it modular home manufacturing, pallet production, or marine construction—demand custom coil nail solutions. Manufacturers offer options including diameter and length adjustments, specialty coatings like epoxy or ceramic for premium rust defense, and personalized collation types such as paper tape or dual-wire for enhanced tool compatibility.
For exterior siding, 1 3 4 coil siding nails and 1 1 2 coil siding nails are frequently requested with double-dipped galvanization, color-matched heads, or ring shank profiles for improved grip. In heavy-load framing, 3 1 2 coil framing nails can be specified with precision tips for minimized wood splitting, and smooth or screw shank variations depending on withdrawal requirements. The capacity for small-batch runs—often within 24-48 hours for urgent orders—represents a strategic advantage for fast-paced general contractors and construction firms.
Application Case Studies: Real-World Performance Insights
Across hundreds of job sites, 15 coil nails and their related lengths have consistently demonstrated robust reliability and operational efficiency. For example, in a recent 54,000-square-foot commercial warehouse project, use of coil framing nails sped up the assembly process by 27%, reducing manual handling and tool downtime. In a coastal residential development, builders chose 1 3 4 coil siding nails with advanced anti-corrosive coatings, achieving 45% fewer callbacks due to siding slippage or fastener corrosion over a 3-year post-installation period.
Pallet manufacturers report that switching from loose nails to coiled 1 1 2 siding nails boosted production throughput by as much as 31% and contributed to a measurable drop in rejected inventory due to misapplied fasteners. Table below summarizes use-case outcomes:
Application | Nail Type | Measured Impact | Timeframe |
---|---|---|---|
Commercial Framing | 15 Coil Nails | +27% Assembly Efficiency | 6 Months |
Coastal Siding Installation | 1 3 4 Coil Siding Nails | -45% Callbacks (Fastener Corrosion) | 3 Years Post-Install |
Pallet Manufacturing | 1 1 2 Coil Siding Nails | +31% Throughput; -22% Rejection Rate | Annual |
Heavy Timber Framing | 3 1 2 Coil Framing Nails | +15% Withdrawal Resistance (vs. Strip Nails) | 8 Months |
These empirical results reinforce the performance and versatility of coil nail technology under demanding conditions and reinforce its growing adoption among construction professionals.
Market Trends: Growth Statistics and Industry Demands
The global market for coil nails is witnessing rapid evolution, fueled by shifts in construction techniques, labor optimization, and sustainability directives. Industry reports indicate that worldwide demand for all coil nail varieties—including 15 coil nails—will chart a CAGR of 5.4% through 2028, reaching a projected value of $7.8 billion. Growth is especially notable in modular building, home improvement, and pallet logistics sectors.
Increasing emphasis on environmentally-friendly building materials is spurring innovation in nail coatings and recyclability. Over 68% of North American contractors now cite automated or pneumatic nailing systems as a primary purchasing driver for fasteners, and the shift toward coated and collated nails has outpaced traditional loose nails by nearly 3:1. Customized ordering platforms and just-in-time supply chain solutions are becoming expected as end-users demand rapid fulfillment on top of specification accuracy.
Conclusion: Why 15 Coil Nails Remain a Leading Choice
In conclusion, the sustained preference for 15 coil nails and their related specifications—such as 1 3 4 coil siding nails, 1 1 2 coil siding nails, and 3 1 2 coil framing nails—stems from technical innovation, robust manufacturer support, and tangible field results. With superior holding power, efficient automation compatibility, and customizable options, these fasteners set industry standards for quality and performance.
As construction and manufacturing landscapes continue to evolve, coil nails will remain at the forefront of fastening solutions, delivering value through durability, adaptability, and data-proven outcomes. For contractors and procurement specialists seeking a reliable partner in fastening technology, 15 coil nails offer both legacy reliability and readiness for tomorrow’s projects.

(15 coil nails)