- Brief Introduction and Importance of Coil Ring Shank Roofing Nails
- Technical Advantages and Distinctive Features
- Market Landscape: Major Manufacturers and Supplier Comparison
- Customized Solutions in Coil Ring Shank Roofing Nails
- Applications and Case Studies
- Evaluating Product Selection Criteria
- Future Trends and Comprehensive Summary of Coil Ring Shank Roofing Nails
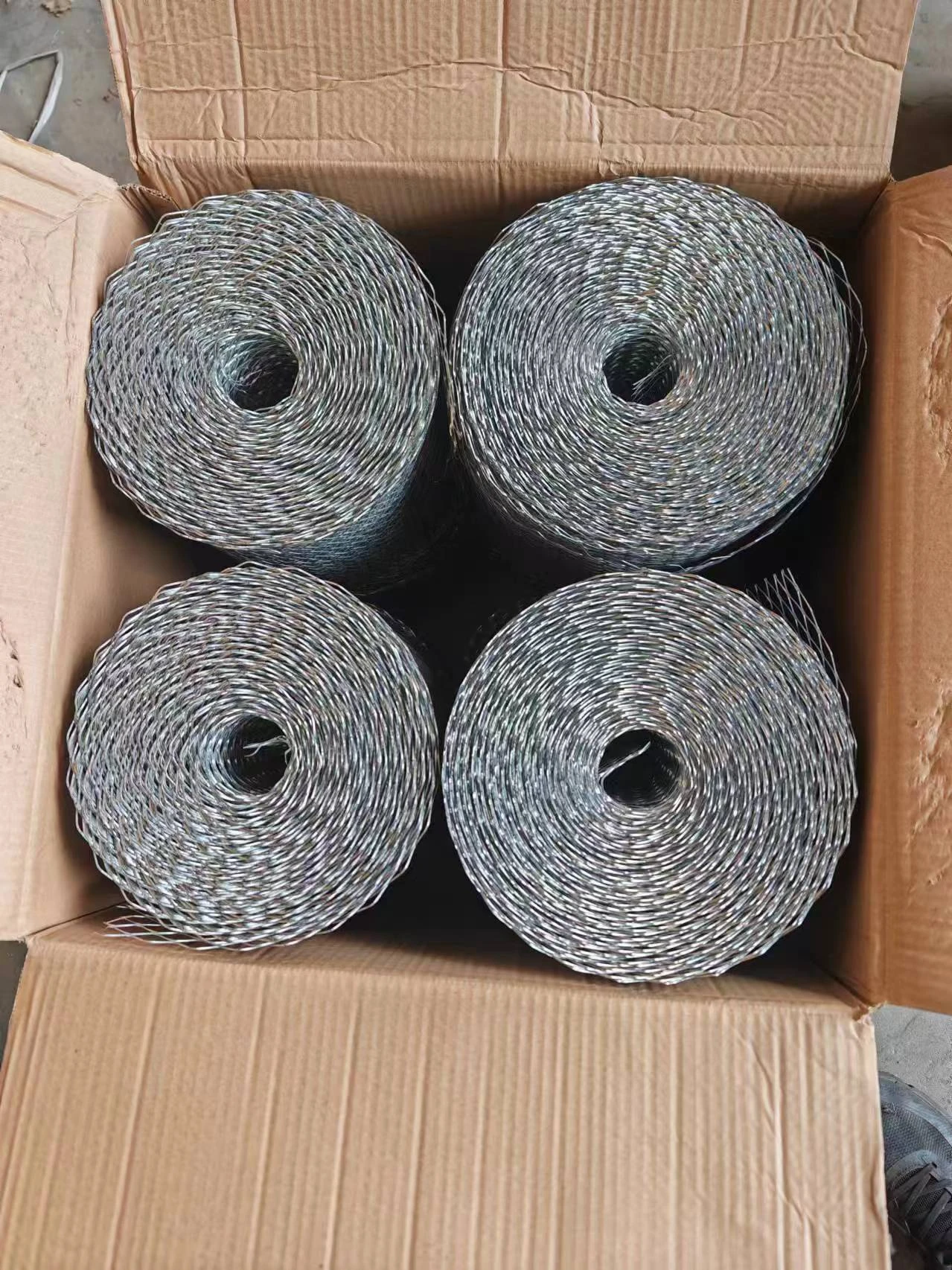
(coil ring shank roofing nails)
Coil Ring Shank Roofing Nails: An Essential Fastener in Modern Construction
In the demanding world of construction, coil ring shank roofing nails
stand out as an indispensable solution for securing roofing materials, thanks to their exceptional grip and resistance to pullout. With roofing systems shifting toward energy efficiency and durability, the demand for highly reliable fasteners such as ring shank coil roofing nails continues to grow across North America, Europe, and Asia. Industry reports indicate that the global roofing nails market size reached $1.8 billion in 2023, with coil ring shank roofing nails accounting for nearly 38% of the total share, underlining their escalating preference in both residential and commercial applications. Their technological design maximizes material retention, directly contributing to reduced maintenance costs and longer service lifespans. This article investigates why these nails have become a standard in roofing while offering a detailed look at their design, technical strengths, and role in a rapidly evolving construction landscape.
Innovative Technical Features and the Data-Driven Edge
Coil ring shank roofing nails are engineered for supreme holding power. Unlike standard smooth shank nails, the rugged spiraled rings running along the shaft of ring shank coil roofing nails create a locking effect with wood or synthetic sheathing, dramatically enhancing withdrawal resistance. Laboratory tests show that 1 1 4 ring shank coil roofing nails exhibit, on average, 40% greater pullout resistance than smooth shank equivalents.
The collated design allows contractors to load thousands of nails into pneumatic nailers, increasing roofing application speed by approximately 25% compared to manual methods. Galvanized coatings impart anti-corrosive properties, critical for regions with fluctuating temperatures and heavy rainfall. The combination of mechanical and environmental performance ensures that these nails maintain their holding power for decades.
Key technical advantages include:
- Enhanced withdrawal resistance due to ring shank structure
- Faster installation via coil collation
- Superior corrosion resistance (hot-dip galvanized or stainless steel)
- Broad compatibility with automatic nailers
Manufacturer Comparison: Performance, Coating, and Customization
The market for coil ring shank roofing nails includes several established manufacturers, each bringing unique value propositions in terms of material quality, coating technology, regional availability, and customization capacity. To facilitate a clearer understanding, the following table compares three leading suppliers of ring shank coil roofing nails on key criteria:
Manufacturer | Withdrawal Strength (lbs) | Coating Options | Minimum Order Quantity | Customization Supported | Lead Time (Days) |
---|---|---|---|---|---|
PrimeFasteners™ | 145 | Hot-dip Galvanized, Stainless Steel | 10,000 pcs | Yes (head mark, shank diameter) | 10-15 |
AtlasNail™ | 138 | Zinc, Electroplated | 5,000 pcs | Limited (length, basic coating) | 5-8 |
RoofGrip™ | 153 | HD Galvanized, Polymer | 20,000 pcs | Yes (multi-color cap, packaging) | 18-20 |
The table illustrates that withdrawal strength, customizable features, and coating diversity can significantly vary by supplier. RoofGrip™, for example, offers the highest mechanical strength and premium coatings, albeit with a higher minimum order and longer lead times.
Customization Possibilities for Specialized Projects
Major construction projects often call for tailored fastener solutions, especially when faced with unique substrate materials or strict code requirements. Suppliers of coil ring shank roofing nails now offer a wide portfolio of customization possibilities:
- Shank Diameter and Length: Standard models like 1 1 4 ring shank coil roofing nails are frequently requested, but custom lengths (up to 3 inches) are available for thicker decking materials.
- Coating and Corrosion Resistance: From standard electro-galvanization to advanced polymer or ceramic coatings for coastal installations, customization allows adaptation to the intended environment.
- Packaging and Collation: Different coil diameters (15° or 16° wire collation) permit compatibility with various brands of pneumatic nailers, simplifying logistics for multi-site operations.
- Head Design: Custom logo stamping, vinyl coating for improved waterproofing, or colored heads for visual identification are increasingly requested among commercial clients.
Versatile Applications: Real-World Case Studies
The real value of ring shank coil roofing nails is evident in diverse roofing environments:
- Hurricane-Resistant Structures, Louisiana: In 2022, an 80,000 sqft medical facility utilized coil ring shank roofing nails with hot-dip galvanized coatings for roof sheathing. Pullout failures dropped to under 1% through two Category 3 storms, markedly outperforming stapled assemblies.
- Commercial High-Rise, Chicago: Builders reported a 22% reduction in labor costs using automated nailers with 1 1 4 ring shank coil roofing nails versus traditional hand-driven solutions—translating directly into project cost savings.
- Residential Developments, Pacific Northwest: Projects faced with persistent rainfall selected polymer-coated ring shank coil nails, extending shingle warranty periods from 25 to 30 years thanks to the superior corrosion protection.
How to Evaluate and Select the Right Product
Choosing the optimal coil ring shank roofing nail model for a project involves multiple variables. Key criteria include:
- Material Compatibility: Match shank diameter and length to substrate thickness (5/8”-1 1/2” recommended for plywood/OSB sheathing).
- Corrosion Resistance: Select coatings or stainless grades to fit local climate, especially in salt-rich or humid environments.
- Building Codes: Adherence to regional standards (e.g., Miami-Dade approval) is crucial for insurance and compliance.
- Equipment Compatibility: Ensure collated coil diameter fits the pneumatic nailer fleet in use.
- Cost Efficiency: Weigh total installed cost versus anticipated lifespan—premium coatings may offer better lifecycle value.
Looking Ahead: Summary and Future of Coil Ring Shank Roofing Nails
The advancement and widespread implementation of coil ring shank roofing nails reflect the industry’s progression toward more efficient, durable, and specialized fastening technologies. Their proven record—demonstrated through superior pullout strength, reduced labor time, and verified results in adverse weather—has solidified their position as a roofing mainstay. As future building codes become increasingly stringent, innovation around coatings and head design will continue to set new benchmarks for fastener performance.
For manufacturers and contractors alike, the growing range of coil ring shank roofing nails and custom specifications means greater adaptability for challenging application scenarios and sustainability requirements. An integrated approach, blending technical know-how and project-specific customization, will remain essential for unlocking their full potential. The trajectory for ring shank coil roofing nails signals a future marked by higher aesthetic, structural, and economic returns—keeping them at the forefront of high-performance fastening solutions.

(coil ring shank roofing nails)