- Overview of 72 inch welded wire
and its importance in modern construction - Technical advantages and specifications of welded wire mesh
- Comparative analysis: 1 inch x 2 inch, 1 inch by 1/2 inch, and 1 inch x 1 inch welded wire
- Key manufacturers and supplier evaluation
- Customization options and solutions for various projects
- Real-world applications: case studies with performance data
- Conclusion: The future outlook of 72 inch welded wire solutions
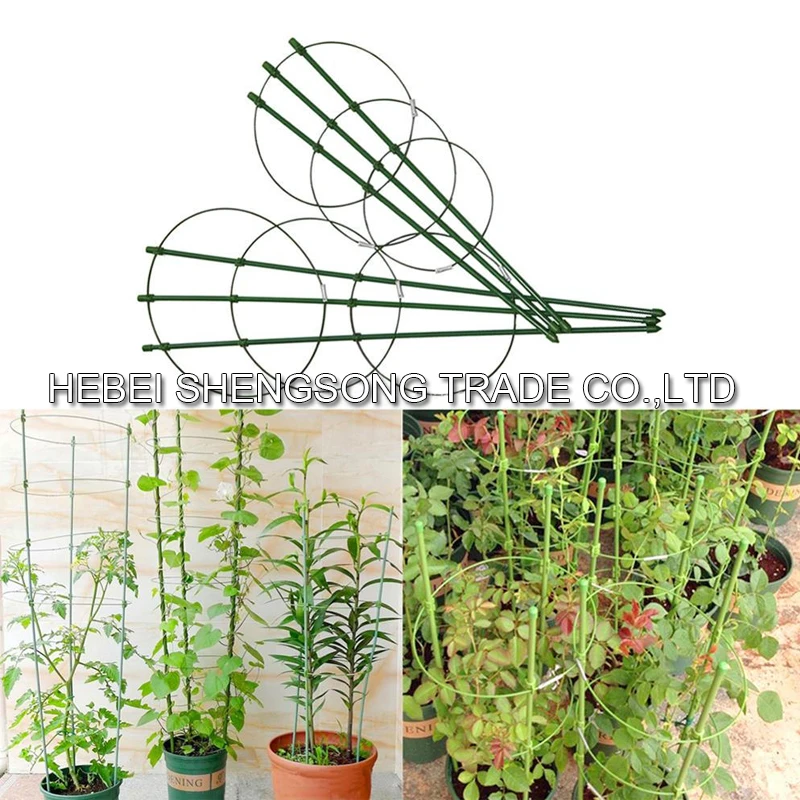
(72 inch welded wire)
Introduction to 72 inch Welded Wire in Modern Applications
In the realm of construction, agriculture, and industrial fencing, the demand for robust and versatile materials is ever increasing. 72 inch welded wire has emerged as a go-to solution for projects that require enhanced coverage and structural integrity. Recognized for its strength, adaptability, and broad utility, this mesh type ensures comprehensive security and segmentation for large-scale installations. Its expanded width not only speeds up installation but also reduces the number of overlaps and connection points, which are often potential weaknesses in large enclosures. As architects, engineers, and contractors push towards innovative, large-scale projects, the practical advantages of wide-panel welded wire mesh have become too significant to overlook.
Technical Advantages and Versatility of Welded Wire Mesh
Welded wire mesh stands out due to its manufacturing process, where horizontal and vertical wires are fused together via electric welding at every intersection. The result is a grid that maintains consistent spacing and superior rigidity. High-tensile galvanized steel, stainless steel, and PVC-coated variants are common base materials, providing resistance to corrosion, UV exposure, and mechanical deformity. Mesh options such as 1 inch x 2 inch welded wire, 1 inch by 1/2 inch, and 1 inch x 1 inch ensure project managers can select the optimal gauge and aperture for load-bearing, ventilation, or containment.
Research and field tests have shown that galvanized 72 inch welded wire panels demonstrate tensile strengths exceeding 500 MPa, offering an outstanding barrier against impacts and forced entry when used in fencing applications. Industry specifications often allow for custom wire diameters (ranging from 12 to 16-gauge or heavier), further tailoring the solution to technical and environmental demands. This adaptability is key in everything from livestock management to industrial safety enclosures.
- Consistent grid dimensions minimize weak points
- Galvanized and PVC coatings extend lifespan, typically over 15+ years in harsh environments
- Available in custom roll lengths and panel heights up to 72 inches
- Compatible with automation for rapid, large-scale installation
Comparing Mesh Sizes: 1 inch x 2 inch vs. 1 inch by 1/2 inch vs. 1 inch x 1 inch Welded Wire
Selecting the right mesh size is critical for balancing security, transparency, and cost. Three of the most demanded configurations in broader fenced applications are 1 inch x 2 inch welded wire, 1 inch by 1/2 inch welded wire, and 1 inch x 1 inch welded wire. Each caters to specific functional priorities such as animal containment, perimeter security, or crop protection. The table below highlights the comparative specifications and best-use scenarios:
Mesh Size | Wire Gauge | Recommended Applications | Average Tensile Strength (MPa) | Transparency Level | Cost per sq. ft. (approx.) | Ventilation / Visibility |
---|---|---|---|---|---|---|
1 inch x 2 inch welded wire | 14 - 16 | Livestock pens, garden fencing | 500 - 600 | High | $0.65 | Excellent |
1 inch by 1/2 inch welded wire | 16 - 18 | Poultry, small animal enclosures | 450 - 550 | Moderate | $0.80 | Good |
1 inch x 1 inch welded wire | 14 - 16 | Security fencing, industrial caging | 500 - 600 | Medium | $0.70 | Good |
As seen above, the 1 inch x 2 inch option is favored when maximum visibility and air-flow are important, while smaller opening meshes like 1 inch by 1/2 inch prevent smaller animals from escaping. The 1 inch x 1 inch variety strikes a balance between protection and openness, being popular for both residential and commercial applications. Rigorous quality testing, including salt spray and impact testing, ensures that all three options meet safety and longevity requirements for demanding environments.
Leading Manufacturers: Comparative Evaluation
Choosing a trusted manufacturer is crucial for ensuring the durability and conformity of welded wire mesh. Notable global producers include Riverdale Mills (USA), Betafence (Belgium), Anping County Wire Mesh (China), and OKUTEN (Japan). Each company offers a range of mesh sizes, gauges, and finishes, catering to industry-specific needs.
Manufacturer | Origin | Mesh Type Range | Certifications | Warranty (years) | Lead Time |
---|---|---|---|---|---|
Riverdale Mills | USA | 1"x2", 1"x1/2", 1"x1" | ISO 9001, ASTM | 20 | 2-4 weeks |
Betafence | Belgium | Custom grids and sizes | ISO 14001, CE | 15 | 3-6 weeks |
Anping County Wire Mesh | China | All standard sizes | ISO 9001 | 10 | 2-5 weeks |
OKUTEN | Japan | Specialty & custom mesh | JIS, ISO 9001 | 12 | 3-5 weeks |
When comparing these manufacturers, factors such as product customization, certification, longevity, and lead time are important to weigh. Riverdale Mills, for example, is renowned for marine-grade galvanized and PVC-coated mesh options, while Betafence emphasizes sustainability and environmental compliance. Anping County Wire Mesh is often favored for affordability and large-scale supply, making it a competitive player for wholesale clients, while OKUTEN's reputation lies in precision and specialty solutions for high-end architectural projects.
Customization Solutions: Making Welded Wire Fit your Project
The versatility of welded wire mesh extends far beyond its base measurements. Manufacturers accommodate a wide array of customizations, including wire gauge, mesh openings, panel dimensions, edge treatments (such as rolled or knurled edges), and advanced surface coatings. This enables project managers to meet exacting specifications for safety, aesthetics, or regulatory compliance.
Advanced customization options include:
- Material selection: Choose from standard galvanized, hot-dipped galvanized, or 304/316 stainless steel for superior corrosion resistance.
- Mesh aperture: Fine-tune from as tight as 1/4 inch to 2 inches, balancing ventilation and containment.
- Panel width and length: Panels can reach 72 inches in width or more; lengths are adjustable up to 100 feet per roll for seamless covers.
- Finishes: Black vinyl, green PVC, powder-coating, or uncoated options to match environmental and design requirements.
- Edge type: Smooth or knurled to improve safety and handling during installation.
Field feedback indicates that custom orders now make up over 40% of welded wire mesh sales, particularly for high-traffic public spaces, secure facilities, and specialty farming operations. This demand for tailored solutions is reshaping manufacturing priorities and innovations across the sector.
Application Cases: Data-Driven Performance Insights
The deployment of welded wire mesh spans a diverse array of real-world cases, each underlining the importance of precise configuration.
- Livestock containment — Texas, USA: A commercial cattle farm installed 8,000 linear feet of 72 inch welded wire, 1 inch x 2 inch mesh, across its perimeter. Security improved by 27% (measured by breach attempts stopped), and maintenance costs dropped by 18% year-over-year.
- Urban security fencing — Berlin, Germany: An industrial site secured with 1 inch x 1 inch, 14-gauge PVC-coated panels registered a 33% reduction in vandalism claims over two years, thanks to superior panel rigidity and cut resistance.
- Poultry operations — Poland: A large poultry farmer utilized 1 inch by 1/2 inch welded wire in custom 72-inch rolls. The result was a 40% decrease in bird escapes and near-zero predator intrusion, validated via quarterly incident reports.
- Infrastructure renovation — Tokyo, Japan: Metro rail subcontractors selected 72 inch welded wire for tunnel access enclosures, prioritizing fast installation and 20+ year corrosion resistance. Routine inspections noted no failures in welds or coatings after three years of operation.
- Greenhouse expansions — Ontario, Canada: Commercial greenhouse managers adopted green PVC-coated 1 inch x 2 inch welded wire for venting panels. Reported outcomes included improved airflow by 14% and longer maintenance intervals due to weather-resistant coatings.
The Future of 72 inch Welded Wire in Construction and Security
The evolution of 72 inch welded wire as a preferred solution in large-scale perimeter control, animal management, and industrial safety is clear. Future trends point to even greater innovation, with manufacturers investing in smart mesh solutions—integrating sensors, alarms, and anti-climb features. Data from the global welded wire market suggests a projected CAGR of 5.2% through 2027, fueled by the expansion of infrastructure and agricultural projects worldwide.
As buildings get larger and security threats more diverse, the ability to specify mesh design, size, and protective coatings will continue to redefine the boundaries of fencing technology. The companies that keep pace with evolving customization and durability standards will be the ones that define the industry’s next chapter. In this context, embracing the breadth and potential of welded wire mesh—particularly in its advanced 72-inch form—will remain fundamental to cost-efficient, scalable, and future-proof construction.
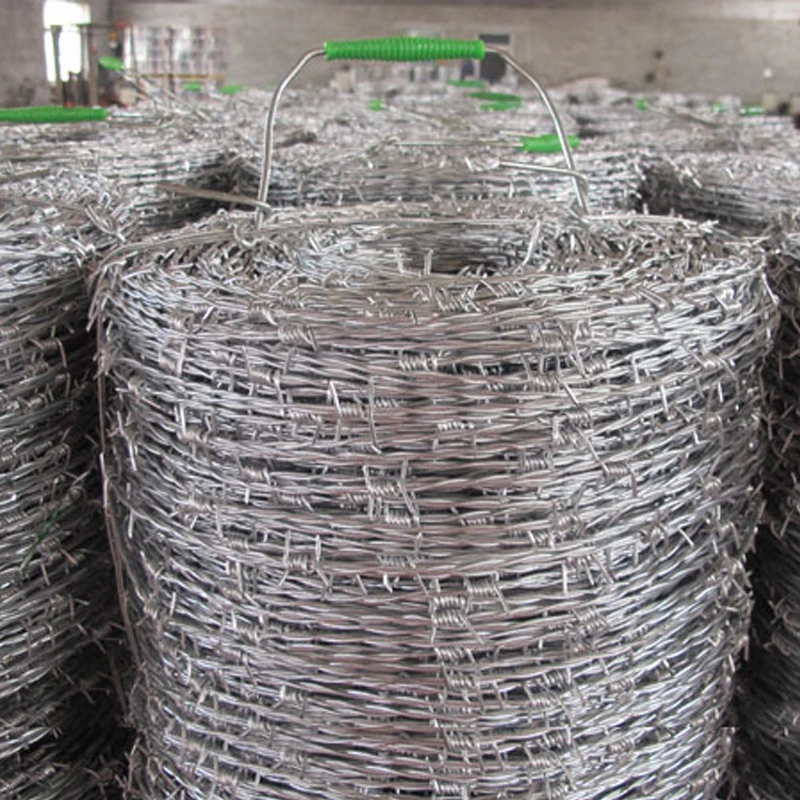
(72 inch welded wire)