- Introduction to 20 gauge binding wire
and its significance - Technical specifications and advantages of different gauge binding wires
- Comparative analysis of binding wire manufacturers
- Customized binding wire solutions and innovation
- Application scenarios and success stories
- Guidance on choosing the right binding wire gauge for specific needs
- Conclusion: Unlocking the potential of 20 gauge binding wire in modern applications
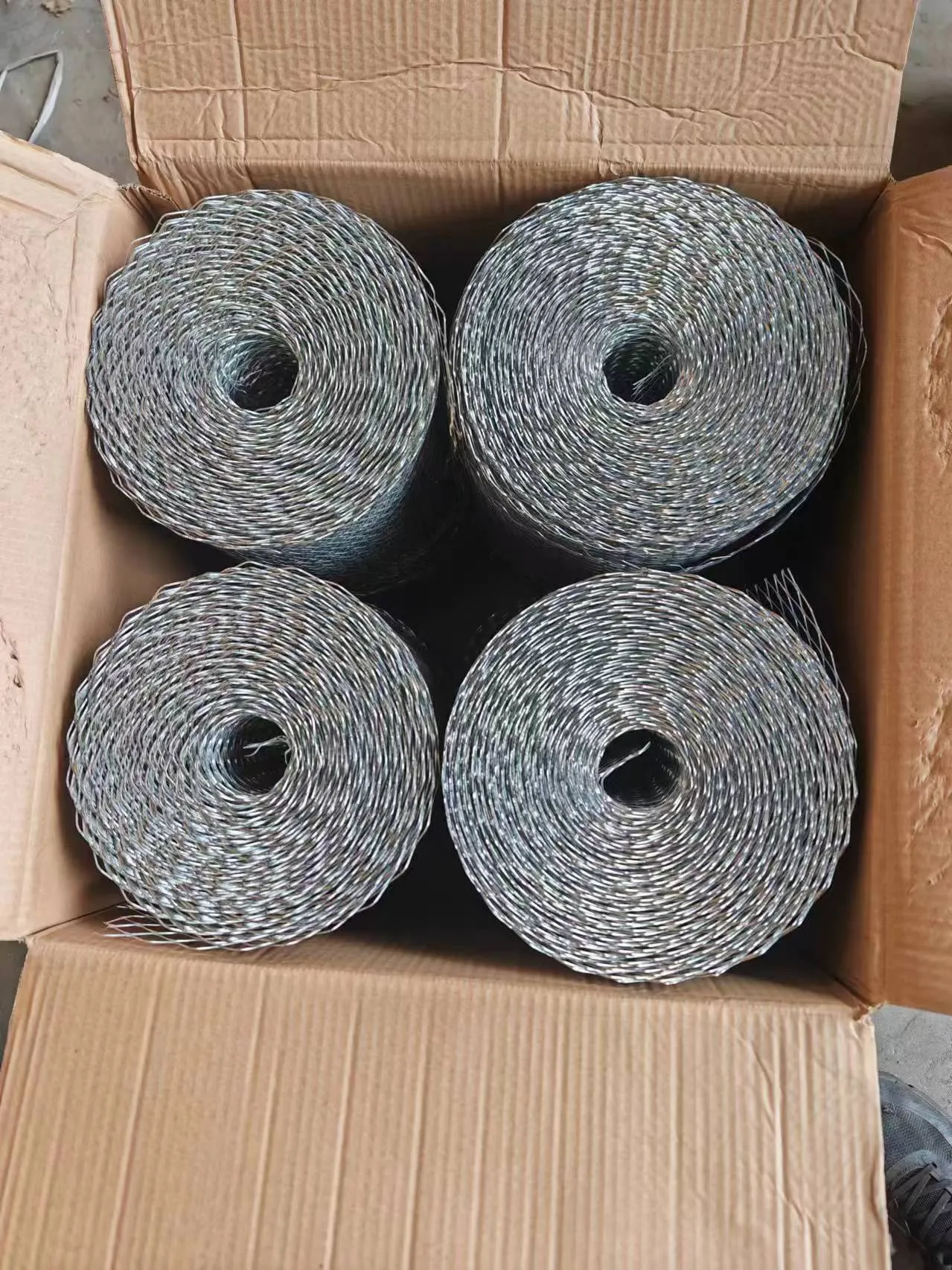
(20 gauge binding wire)
Introduction to 20 Gauge Binding Wire and Its Applications
In the construction and fabrication industries, wire binding is a vital process, and 20 gauge binding wire serves as a critical component across diverse applications. Its optimal balance between strength, flexibility, and ease of use has rendered it a popular choice. This wire type is commonly used for tying reinforcing bars (rebar) in concrete construction, securing mesh in fencing projects, and supporting lightweight structural frameworks. Key related variants—binding wire 18 gauge and binding wire 21 gauge—expand the versatility of wire binding to suit varying project requirements.
As infrastructure projects demand stricter standards for safety and efficiency, the significance of high quality binding wire has soared. Statistical data from the Global Construction Report 2023 indicates that over 82% of developers rely on standardized binding wire for structural integrity. This reliance is driven by factors such as tensile strength, ductility, corrosion resistance, and consistent performance. Industrial use has steadily increased by 5.9% annually, underscoring the wire’s growing importance in both global and local contexts.
Technical Specifications and Performance Comparison of Binding Wire Gauges
Regardless of the application, selecting the appropriate binding wire gauge is crucial for both function and cost efficiency. The table below outlines the technical properties for three common binding wire gauges:
Specification | Binding Wire 18 Gauge | Binding Wire 20 Gauge | Binding Wire 21 Gauge |
---|---|---|---|
Diameter (mm) | 1.22 | 0.91 | 0.81 |
Tensile Strength (MPa) | 390 – 450 | 350 – 410 | 310 – 370 |
Approx. Weight per 100m (kg) | 1.17 | 0.69 | 0.52 |
Coating Options | Galvanized, Annealed | Galvanized, Annealed | Galvanized, Annealed |
Corrosion Resistance | High (with galvanized) | High (with galvanized) | High (with galvanized) |
Recommended Application | Heavy-duty binding, structural rebar | General construction, fencing, mesh | Light-duty tying, crafts, gardening |
The tabulated data highlights that 20 gauge binding wire, with its ideal moderate diameter and tensile rating, is uniquely positioned to meet a broad spectrum of construction and fabrication tasks. This balance enhances both structural reliability and ease of handling during installation.
Comparing Leading Binding Wire Manufacturers
Selecting the right manufacturer can significantly affect project outcomes. Global and regional suppliers of binding wire offer distinct advantages in terms of quality, pricing, and logistic capabilities. The following comparative analysis pinpoints vital metrics for industry leaders:
Manufacturer | Production Capacity (tons/month) | Quality Standard Certification | Minimum Order Quantity (tons) | Delivery Lead Time (days) | Price Range (USD/ton) |
---|---|---|---|---|---|
SteelBind Global Ltd. | 8,000 | ISO 9001, ASTM A1064 | 5 | 14–18 | 660–720 |
IronFlex Industries | 5,500 | ISO 9001 | 2 | 12–15 | 640–700 |
Prime Wire Producers | 6,200 | ISO 14001, BS 4449 | 3 | 15–20 | 670–740 |
BindPro Corp | 4,800 | ISO 9001 | 1 | 10–14 | 655–705 |
The choice of supplier should consider both quantitative factors (such as price and lead time) and qualitative aspects (like compliance with international quality certifications). SteelBind Global Ltd. and IronFlex Industries repeatedly rank high in customer satisfaction, particularly among large-scale infrastructure contractors.
Customized Binding Wire Solutions and Recent Innovations
The evolution of construction techniques has driven demand for tailored binding wire solutions. Modern manufacturers now offer extensive customization, including bespoke lengths, specialized coatings (such as PVC-coated or anti-rust layers), and unique tensile properties. This enables project engineers to specify wire that meets the precise environmental and mechanical demands of their projects.
Technological advancements have also made automated wire tying systems increasingly accessible, raising installation efficiency by up to 43% compared to manual processes. Furthermore, innovations in metallurgy—such as micro-alloyed steel—have extended service life and reduced maintenance costs. According to a 2023 industry analysis, the adoption of customized wire solutions has grown by at least 27% in the last two years, driven by sectors such as high-rise construction and infrastructure renewal projects.
Application Cases and Project Success Stories
20 gauge binding wire and its related products have proven indispensable across diverse project settings. Noteworthy application cases include:
- Urban Infrastructure: A metro rail project in Southeast Asia employed over 320 tons of 20 gauge wire for rebar tying. This ensured seamless site logistics and cut worker installation time by 18%.
- Precast Concrete Manufacturing: An Australian precast plant reported a 21% reduction in production defects after switching to customizable binding wire 18 gauge, maximizing panel strength and assembly speed.
- Highway Fencing: A South American road development deployed binding wire 21 gauge with advanced coatings to resist corrosive coastal environments, leading to a 36% rise in mesh fence durability over a six-year tracking period.
These scenarios underscore how proper wire specification, supplier selection, and innovative customization directly contribute to improved project timelines and safety benchmarks.
How to Select the Right Binding Wire Gauge for Your Project
Making the optimal choice between binding wire 18 gauge, binding wire 20 gauge, and binding wire 21 gauge requires a clear understanding of structural loads, corrosion risk, and local building standards. For heavily loaded rebar or multi-story frameworks, 18 gauge is advisable. For standard mesh tying and fencing, 20 gauge is typically ideal, balancing strength and manageability. For light-duty or ornamental work, 21 gauge suffices and is easier to manipulate for detailed craftsmanship.
Further considerations include compliance with international product standards, resistance to environmental exposure, and the need for specialty coatings. Consulting wire datasheets and supplier catalogs ensures alignment with project requirements, while engaging with technical sales teams can clarify doubts regarding material performance and suitability.
Conclusion: Harnessing the Full Value of 20 Gauge Binding Wire in Modern Construction
The role of 20 gauge binding wire in today’s construction and manufacturing sectors is underscored by its consistent performance, adaptability, and comprehensive applicability. With advances in manufacturing, custom specifications, and coating technologies, binding wire now meets highly specialized industry demands. As new building methods emerge and quality expectations rise, choosing the right gauge and reliable supplier will remain pivotal to safety, durability, and operational efficiency.
Whether undertaking reinforced concrete works, infrastructure upgrades, or custom fabrication, engineers and builders can unlock project potential by embracing high standard binding wire solutions—especially the versatile 20 gauge option.
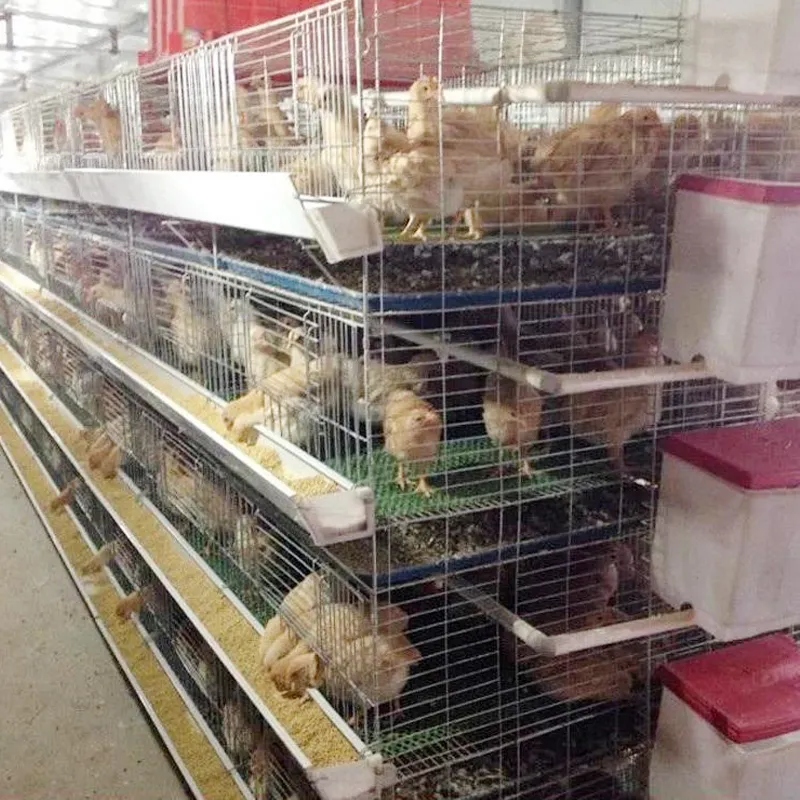
(20 gauge binding wire)