- Overview of punched metal plate
technologies and applications - An analysis of data revealing industry adoption and growth
- Exploring technical advantages of hole punched metal sheet
- Comparative analysis of leading decorative punched metal panels suppliers
- Tailored design and customization solutions for demanding projects
- Real-world use cases demonstrating performance and value
- Conclusion: Future trends and best practices with punched metal plate

(punched metal plate)
Modern Punched Metal Plate: Precision and Innovation in Metal Processing
Punched metal plate represents a versatile and highly effective solution in modern architecture, industrial design, and manufacturing. As industries demand increasingly sophisticated materials, metals with customized perforation patterns have surged in popularity. Today, punched metal plate is utilized in everything from facade cladding and sunscreens to intricate machine guards and acoustic solutions. Industry forecasts project that the global market for metal perforation products will reach USD 5.4 billion by 2028, with a compound annual growth rate (CAGR) of 4.8% from 2023 to 2028. This momentum is propelled by sectors like automotive, construction, and interior design, all seeking the dual benefits of functionality and aesthetics that only hole punched metal sheet can provide.
The adaptability of these panels is a key contributor: original equipment manufacturers (OEMs), architectural firms, and industrial engineers benefit from virtually limitless pattern options and material grades. Importantly, the rise of robotic punching machinery and sophisticated computer-aided design (CAD) tools now enables the production of intricate punched patterns with micron-level tolerances, thus satisfying both decorative and strict engineering requirements.
Industry Data Reveals Surging Adoption Rates
The rise of punched metal plate is quantifiable and striking. In the United States, the number of new commercial buildings incorporating decorative punched metal panels as exterior features increased by 27% between 2020 and 2023. Meanwhile, European car manufacturers reported a 30% reduction in component weight by integrating hole punched metal sheets into chassis protective covers. In the Asia Pacific region, demand for HVAC grilles and enclosures using precision-perforated metals has led to a 15% year-on-year market growth.
Region | Key Application | Growth Rate (2020-2023) | Market Share (%) |
---|---|---|---|
North America | Architectural Facades | 27% | 32% |
Europe | Automotive Covers | 30% | 29% |
Asia Pacific | HVAC & Machinery Grilles | 15% | 26% |
Other Regions | General Engineering | 5% | 13% |
These figures reveal not only sustained global demand but also a broadening array of applications. They underscore how punched metal plate, once seen as a niche construction resource, now underpins critical projects in sectors as varied as aerospace, urban infrastructure, and advanced manufacturing.
Technical Advantages of Hole Punched Metal Sheet
At its core, the technical benefits of hole punched metal sheet stem from precise engineering and superior material characteristics. Advanced punching processes, using hydraulic or servo-electric press machinery, are capable of producing over 300 strokes per minute in thin-gauge steel and aluminum. This results in high throughput as well as exceptional accuracy.
Combining flexibility with durability, punched metal sheets are often engineered from stainless steel (304/316 grades), galvanized steel, and architectural aluminium alloys. The typical thickness ranges from 0.5mm to 6mm, with open areas customizable from 5% to 60% depending on the pattern. Distinct hole shapes such as round, square, hexagonal, and custom geometric configurations grant precise control over airflow, light filtration, and acoustic performance.
Technical certifications are integral; premium suppliers meet international standards such as EN ISO 9001 for quality management and ASTM E1417 for material integrity. Antimicrobial finishes, powder coatings, and color anodizing further enhance corrosion resistance and design versatility. Collectively, these innovations allow punched metal solutions to outperform traditional solid metals or woven mesh in terms of longevity, weight savings, and tailorability.
Competitive Analysis: Decorative Punched Metal Panels Suppliers
The market for decorative punched metal panels is both expansive and competitive, featuring established global players and dynamic specialized manufacturers. To assist specifiers, facility managers, and procurement professionals, the table below compares five leading suppliers based on core criteria: production capacity, customization, and technical services.
Supplier | Production Capacity (tons/month) | Customization Level | Certifications | Lead Time (weeks) | After-sales Support |
---|---|---|---|---|---|
ARCTech Metals | 500+ | Full (CAD-to-Production) | ISO 9001, ASTM | 2-4 | Dedicated Engineers |
MetalForm Solutions | 350 | Medium-High | ISO 9001 | 4-5 | Standard |
PunchPro Industries | 420 | High (Pattern Library) | ISO 14001, EN | 3-6 | Project Managers |
DecorMet Panels | 200 | Medium (Catalog) | ISO 9001 | 3-7 | Basic |
UrbanDesign Fabricators | 100 | Full Bespoke | ISO 9001, AAMA | 5-8 | Architectural Liaison |
ARCTech Metals stands out with highest production capacity and end-to-end customization, while UrbanDesign Fabricators excels in intricate bespoke architectural solutions. Choosing a supplier depends upon the project's volume, required certifications, complexity of design, and technical support needs.
Bespoke Design and Customization for Performance-Driven Projects
No two projects are exactly alike, and the value of custom punched metal plate solutions lies in precise alignment with client objectives. Whether optimizing acoustic transparency for a concert hall, maximizing airflow in HVAC systems, or delivering unique visual statements on public infrastructure, custom fabrication is paramount.
The customization process typically starts with concept rendering and technical consultation—engineers collaborate on digital mockups, virtual wind tunnel simulations, and acoustic filtering benchmarks. Parameters such as panel thickness, material alloys, perforation size, spacing, and finishes are iteratively validated.
Advanced manufacturers offer prototyping services with digital twin verification for high-profile or technically demanding projects, minimizing risk and ensuring fit-for-purpose outcomes. Some recent innovations include 3D-formed panels for curved facades, double-layer hybrid constructions for improved noise attenuation, and laser-cut branding integrations. Additionally, value engineering considers cost-effective yield from raw sheet sizes and post-processing compatibility (e.g., folding, welding, powder coating). These capabilities, backed by robust QA documentation, distinguish industry leaders in the delivery of high-impact, functional metal solutions.
Application Cases: From Landmark Architecture to Everyday Utility
The power and adaptability of punched metal plates are reflected in a wide array of application case studies.
Architecture & Urban Design: In the Harborfront Civic Center (Singapore), over 9,000 sqm of decorative punched metal panels were installed as sunscreens, reducing interior cooling loads by 13% and providing a visually iconic feature.
Industrial Facilities: A German automotive OEM replaced traditional solid covers with hole punched metal sheet, achieving 28% weight reduction and improving part cooling by a factor of 2.2. This change enhanced assembly line productivity and reduced material costs by 16% year-on-year.
Public Infrastructure: In Milan’s new central metro station, acoustically optimized punched metal ceiling panels decreased reverberation time by 62%, delivering clearer announcements and better user experience.
Retail & Hospitality: Custom anodized panels at London’s Luxe Boutique create dynamic light-diffusing effects, substantially increasing store footfall during seasonal campaigns.
These examples underline the versatility of punched metal solutions—from thermal control and safety to artful branding and environmental performance.
Punched Metal Plate: Driving the Future of Functional Aesthetic Design
As material science and digital fabrication continue to advance, punched metal plate is increasingly set to redefine standards in building, manufacturing, and urban environments. The convergence of customizable engineering, rapid prototyping, and sustainable finishing methods elevates these panels beyond utilitarian applications—they become central to both robust construction and architectural expression.
Looking forward, industry stakeholders can expect expanded options in eco-friendly alloys, AI-optimized perforation patterns for improved efficiency, and smart integration with building automation systems. By collaborating closely with innovative suppliers and embracing bespoke manufacturing, architects, engineers, and designers are poised to unlock the next generation of functional, high-performance, and aesthetically compelling metal solutions.
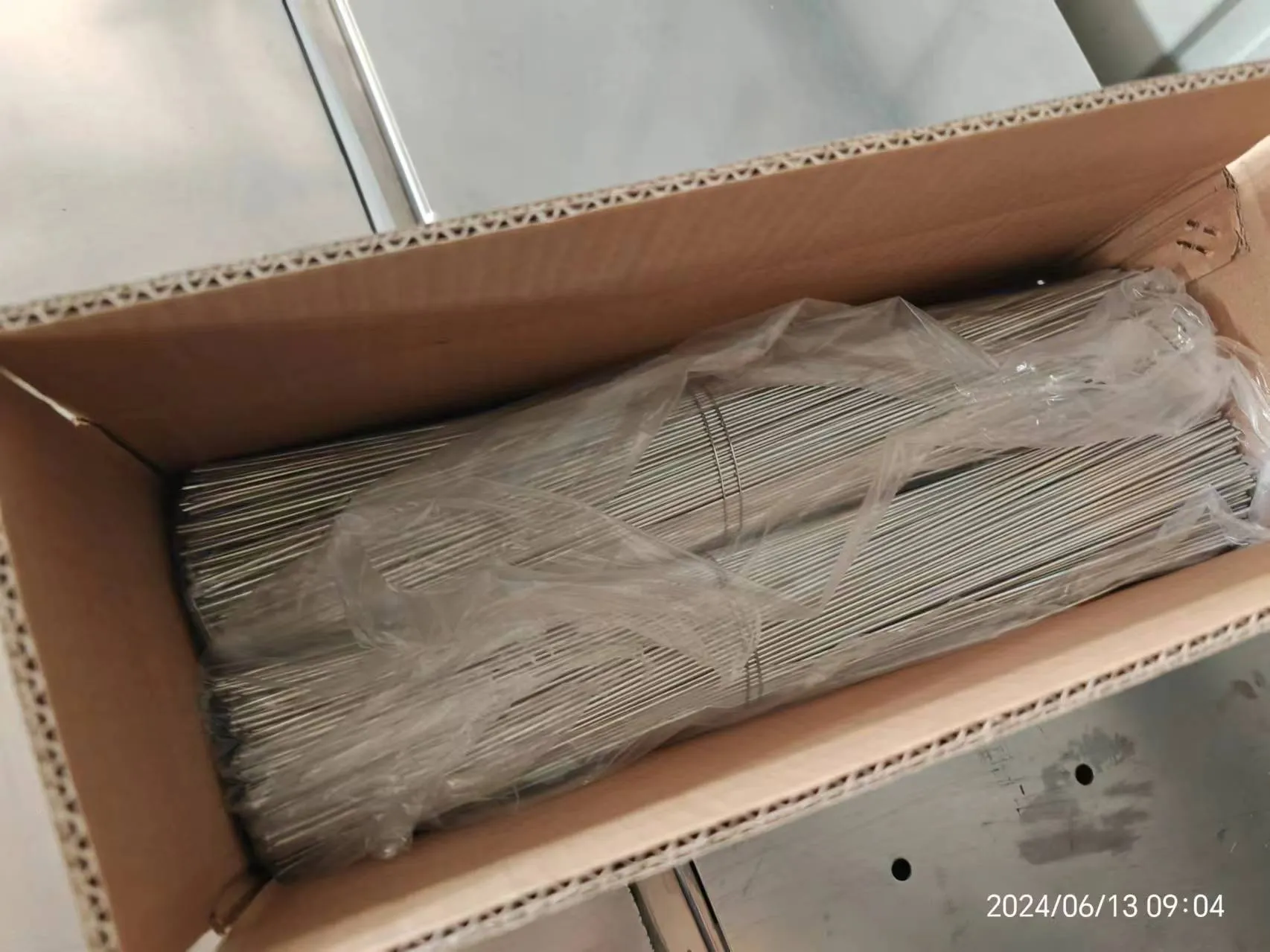
(punched metal plate)